27.5 Rubber and Other Elastomers
Learning Objectives
By the end of this section, you will be able to:
- Acknowledge the history of rubber’s discovery and commercialization.
- Know the properties of rubber.
- Describe the process of vulcanization.
- Describe synthetic rubber.
Natural Rubber
Natural rubber, also called India rubber or caoutchouc consists of polymers of the organic compound isoprene. Isoprene is a butadiene monomer (two carbon-carbon double bonds in the molecule). Isoprene is 2-methyl-1,3-butadiene (Hein et al., 2014). These isoprene-based polymers along with minor impurities of other organic compounds and water form natural rubber. The rubber tree (Castilla elastica) (Figure 27.5a.) is a large tree indigenous to Central America. Its bark produces a stretchy material called latex (“Ancient Mesoamericans”, 2020). The latex is a sticky, milky colloid drawn off by making incisions in the bark and collecting the fluid in vessels in a process called “tapping”. The latex then is refined into rubber ready for commercial processing. Indigenous groups from Mesoamerica determined that mixing the latex from the rubber tree with the juice from the Ipomoea alba plant produced a firm bouncy solid (“Ancient Mesoamericans”, 2020). In major areas, latex is allowed to coagulate in the collection cup. The coagulated lumps are collected and processed into dry forms for marketing. Thailand and Indonesia are currently two of the leading rubber producers in the world.
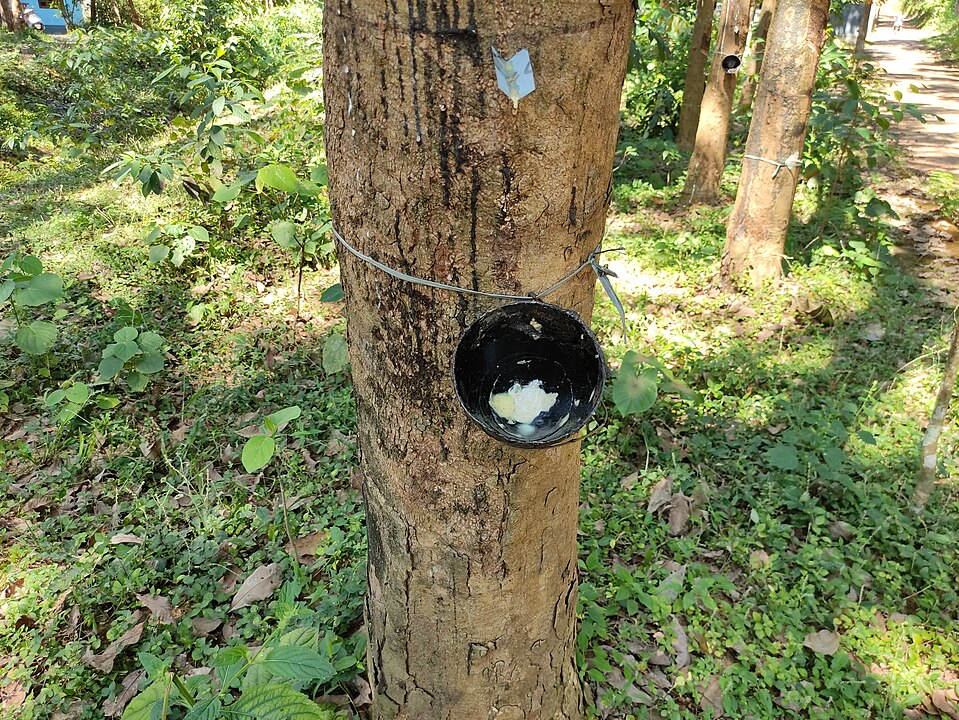
Indigenous Perspectives: Colonialism of Rubber
Learn more about the colonialized history of rubber.
Watch How Your Rubber Ducky Explains Colonialism – YouTube (7 min)
Video source: PBS Origins. (2017, November 8). How your rubber ducky explains colonialism – YouTube [Video]. YouTube.
Forms of polyisoprene that are used as natural rubbers are classified as elastomers. Natural rubber is used extensively in many applications and products, either alone or in combination with other materials. In most of its useful forms, it has a large stretch ratio and high resilience, and is extremely waterproof.

Molecules that have carbon-carbon double bonds can be subject to geometric isomerization. This is also true of polymers with carbon-carbon double bonds. Isoprene and other synthetic butadiene polymers can have cis and trans versions resulting in different spatial orientations and properties. Cis-polyisoprene (as shown in Figure 27.5b.) is found in natural rubber. Trans-polyisoprene is called gutta-perch and is used in electrical insulation, dentistry and golf balls (Hein et al, 2014).
Vulcanization
In 1832–1834 Nathaniel Hayward and Friedrich Ludersdorf discovered that rubber treated with sulfur lost its stickiness. It is likely Hayward shared his discovery with Charles Goodyear, possibly inspiring him to make the discovery of vulcanization. Thomas Hancock (1786–1865), a scientist and engineer, was the first to patent vulcanization of rubber. He was awarded a British patent on May 21, 1845. Three weeks later, on June 15, 1845, Charles Goodyear was awarded a patent in the United States. It was Hancock’s friend William Brockedon who coined term ‘vulcanization’. Goodyear claimed that he had discovered vulcanization earlier, in 1839.
Sulfur vulcanization is a chemical process for converting natural rubber or related polymers into more durable materials by heating them with sulfur or other equivalent curatives or accelerators. The term vulcanization is derived from Vulcan, the Roman god of fire. Sulfur forms cross-links (bridges) between sections of polymer chain which results in increased rigidity and durability, as well as other changes in the mechanical and electronic properties of the material. Vulcanization requires the presence of a carbon-carbon double bond in the polymer structure. The presence of the carbon-carbon double bond can result to age hardening and cracking of tires due to ozone attack. By vulcanizing the rubber, the useful temperature range of the rubber products and increases the abrasion resistance (Hein et al, 2014). A vast array of products are made with vulcanized rubber, including tires, shoe soles, hoses, and conveyor belts. Figure 27.5c. shows the ideal of sulfur cross-links and the chemical structure of vulcanized polyisoprene.
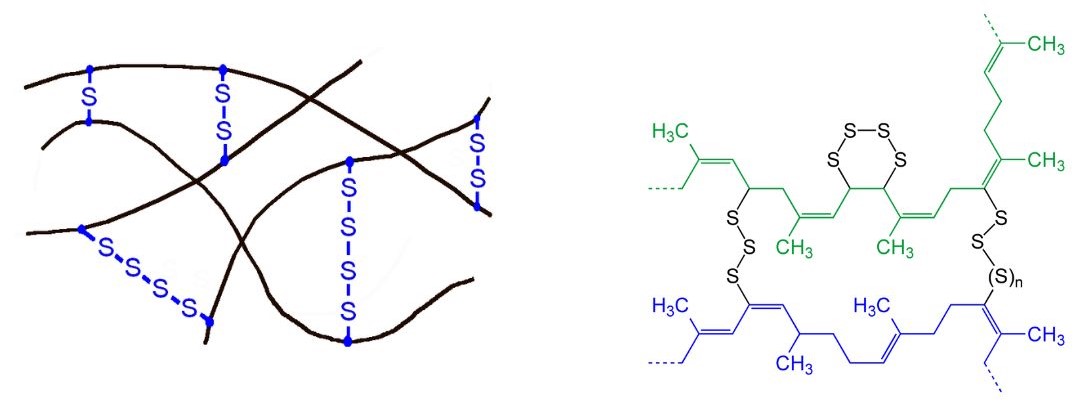
Synthetic Rubber
The expanded use of bicycles, and particularly their pneumatic tires, starting in the 1880s, created increased demand for rubber. In 1909 a team headed by Fritz Hofmann, working at the Bayer laboratory in Germany, succeeded in polymerizing isoprene, the first synthetic rubber. A synthetic rubber is any artificial elastomer. These are mainly polymers synthesized from petroleum byproducts.
Polybutadiene rubber is a polymer formed from the polymerization of the monomer 1,3-butadiene. Polybutadiene has a high resistance to wear and is used especially in the manufacture of tires, which consumes about 70% of the production. Another 25% is used as an additive to improve the toughness (impact resistance) of plastics such as polystyrene and acrylonitrile butadiene styrene (ABS). Polybutadiene rubber accounted for about a quarter of total global consumption of synthetic rubbers in 2012. It is also used to manufacture golf balls, various elastic objects and to coat or encapsulate electronic assemblies, offering high electrical resistivity. Figure 27.5d. shows the trans and cis versions of 1,4-polybutadiene

Neoprene (also polychloroprene or pc-rubber) is a family of synthetic rubbers that are produced by polymerization of chloroprene (2-chloro-1,3-butadiene). Neoprene exhibits good chemical stability and maintains flexibility over a wide temperature range. Neoprene is sold either as solid rubber or in latex form and is used in a wide variety of applications, such as laptop sleeves, orthopedic braces (wrist, knee, etc.), electrical insulation, liquid and sheet applied elastomeric membranes or flashings, and automotive fan belts. Neoprene is produced by free-radical polymerization of chloroprene. In commercial production, this polymer is prepared by free radical emulsion polymerization (Figure 27.4e.). Polymerization is initiated using potassium persulfate. Bifunctional nucleophiles, metal oxides (e.g. zinc oxide), and thioureas are used to crosslink individual polymer strands.
-
Figure 27.4e. Free radical synthesis of neoprene from 2-chloro-1,3-butadiene. (Credit: Photo by Rifleman 82, PDM)
Styrene-butadiene or styrene-butadiene rubber (SBR) describe families of synthetic rubbers derived from styrene and butadiene. SBR is an example of a copolymer where two different kind of monomer units are combined in a specific ratio (not necessarily 1:1) (Hein, 2014). Figure 27.4f. shows the structure of styrene-butadiene polymer showing repeating styrene (aromatic ring) and butadiene (carbon-carbon double bond) units. The version developed by Goodyear is called Neolite. These materials have good abrasion resistance and good aging stability when protected by additives. In 2012, more than 5.4 million tonnes of SBR were processed worldwide. About 50% of car tires are made from various types of SBR. It is a commodity material which competes with natural rubber. The elastomer is used widely in pneumatic tires. Other uses include shoe heels and soles, gaskets, and even chewing gum.
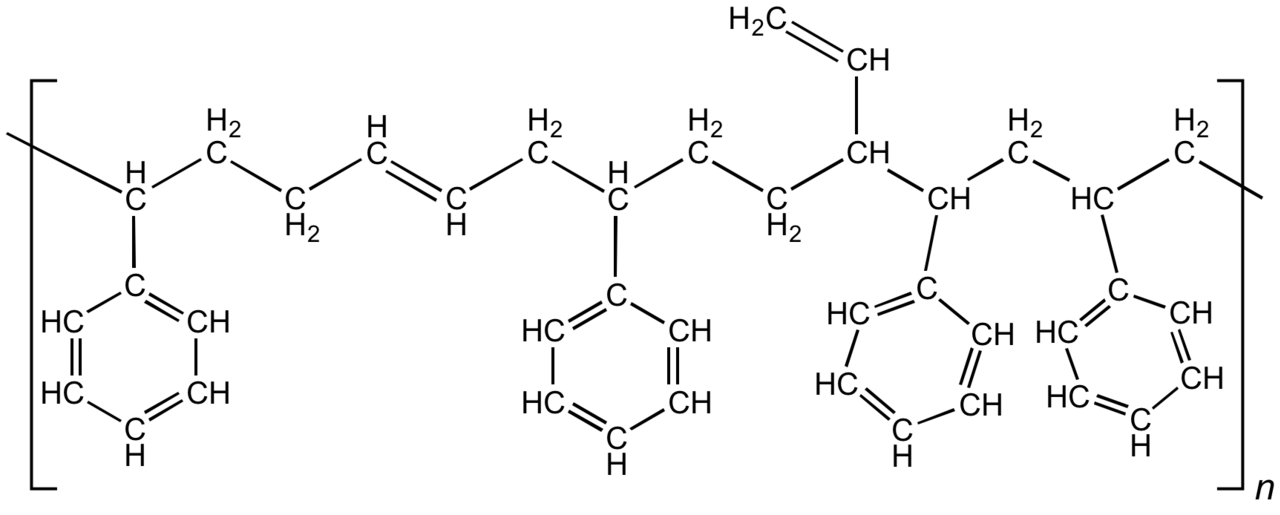
Spotlight on Everyday Chemistry: Athletic Tracks
Rubber and rubber like polymers are used in many places. Athletic running tracks are one example.
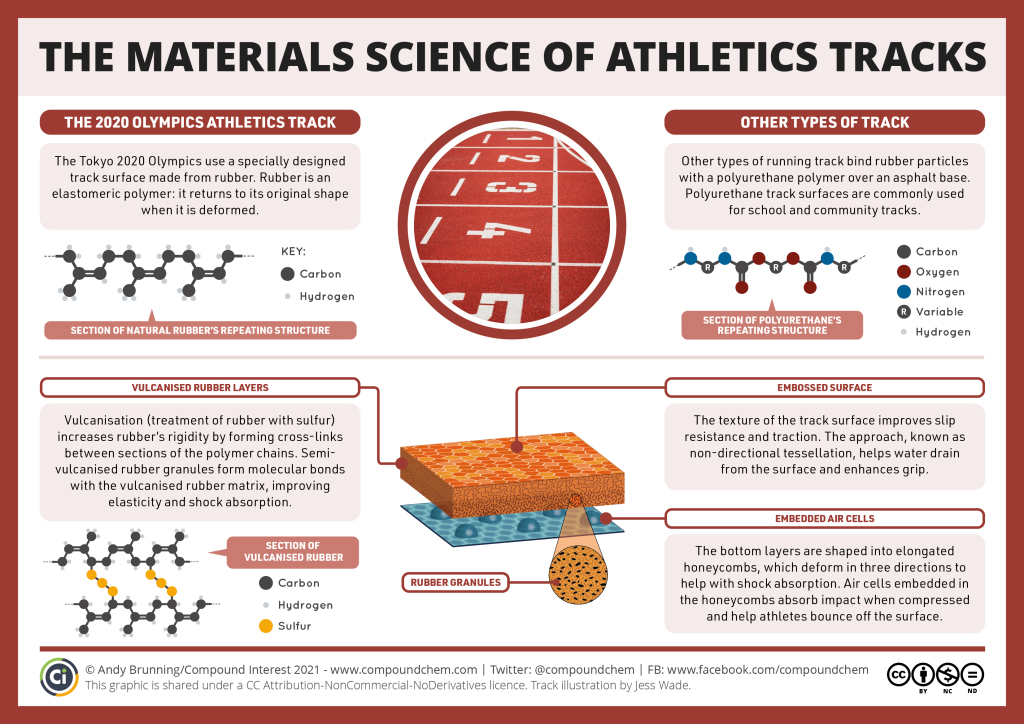
Attribution & References
Except where otherwise noted, this page has been adapted by Samantha Sullivan Sauer from
- “10.4: Rubber and Other Elastomers” In Map: Chemistry for Changing Times (Hill and McCreary) by Marisa Alviar-Agnew (Sacramento City College) & LibreTexts, licensed under CC BY-SA.
References cited in text
Ancient Mesoamericans invented rubber 3,000 years before Goodyear. (2020, January 19). History Daily.
Hein, M., Pattison, S., Arena, S., & Best, L. R. (2014). Introduction to General, Organic, and Biochemistry (11th ed.). Wiley.
polymers with elastic properties
chemical process for converting natural rubber or related polymers into more durable materials by heating them with sulfur or other equivalent curatives or accelerators
polymer formed from the polymerization of the monomer 1,3-butadiene
family of synthetic rubbers that are produced by polymerization of chloroprene
families of synthetic rubbers derived from styrene and butadiene
two or more different monomers that form a polymer in a specific ratio