27.7 Properties of Polymers
Learning Objectives
By the end of this section, you will be able to:
- Describe the physical properties of polymers based on their molecular and intermolecular structures.
- Identify crystalline and amorphous sections of polymers.
- Describe the processing of polymers.
Physical Properties
The physical properties of a polymer such as its strength and flexibility depend on:
- chain length – in general, the longer the chains the stronger the polymer;
- side groups – polar side groups (including those that lead to hydrogen bonding) give stronger attraction between polymer chains, making the polymer stronger;
- branching – straight, unbranched chains can pack together more closely than highly branched chains, giving polymers that have higher density, are more crystalline and therefore stronger;
- cross-linking – if polymer chains are linked together extensively by covalent bonds, the polymer is harder and more difficult to melt.
Example 27.7a
Polymers are used in many toys such as Lego. Over time, the type of polymer used in Lego has changed. Infographic 27.7a. shows the polymer details of some Lego pieces.
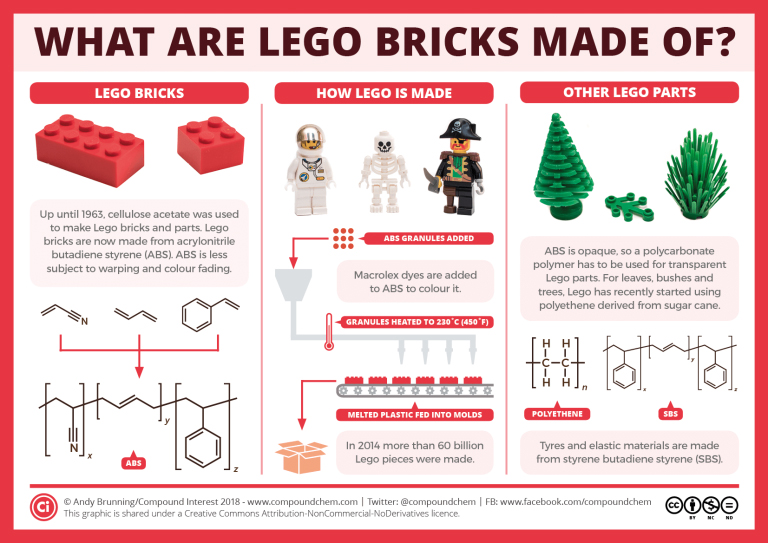
Crystalline and Amorphous Polymers
When applied to polymers, the term crystalline has a somewhat ambiguous usage. A synthetic polymer may be loosely described as crystalline if it contains regions of three-dimensional ordering on atomic (rather than macromolecular) length scales, usually arising from intramolecular folding and/or stacking of adjacent chains as shown in Figure 27.7a.
Synthetic polymers may consist of both crystalline (aligned) and amorphous (random) regions; the degree of crystallinity may be expressed in terms of a weight fraction or volume fraction of crystalline material. Few synthetic polymers are entirely crystalline. The crystallinity of polymers is characterized by their degree of crystallinity, ranging from zero for a completely non-crystalline polymer to one for a theoretical completely crystalline polymer.
Polymers with crystalline regions are generally tougher (can be bent more without breaking) and more impact-resistant than totally amorphous polymers. Polymers with a degree of crystallinity approaching zero or one will tend to be transparent, while polymers with intermediate degrees of crystallinity will tend to be opaque due to light scattering by crystalline or glassy regions.
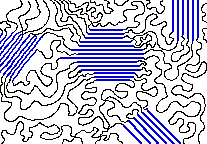
Depending on the degree of crystallinity, there will be a higher melting point at which the crystalline regions come apart and the material becomes a viscous liquid. These are thermoplastic polymers. Such liquids can easily be injected into molds to manufacture objects of various shapes or extruded into sheets or fibers.
Thermosetting polymers (generally those that are highly cross-linked) do not melt at all. If they are to be made into molded objects, the polymerization reaction must take place within the molds — a far more complicated process. About 20% of the commercially produced polymers are thermosets; the remainder are thermoplastics.
Glass Transition Temperature
In thermoplastic polymers, there is a fairly definite softening point that is observed when the thermal kinetic energy becomes high enough to allow internal rotation to occur within the bonds and to allow the individual molecules to slide independently of their neighbours. This renders the polymer more flexible and deformable. This temperature is called the glass transition temperature.
Hard plastics like polystyrene and poly(methyl methacrylate) are used well below their glass transition temperatures, in their glassy state. Their glass transition temperatures are well above room temperature, both at around 100 °C. Rubber elastomers like polyisoprene and polyisobutylene are used above their glass transition temperature, that is, in the rubbery state, where they are soft and flexible.
Processing Polymers
Molding is the process of manufacturing by shaping liquid or pliable raw material using a rigid frame called a mold or matrix. This itself may have been made using a pattern or model of the final object.
Compression molding is a forming process in which a plastic material is placed directly into a heated metal mold then is softened by the heat and therefore forced to conform to the shape of the mold, as the mold closes.
Transfer molding (BrE moulding) is a manufacturing process where casting material is forced into a mold. Transfer molding is different from compression molding in that the mold is enclosed rather than open to the fill plunger resulting in higher dimensional tolerances and less environmental impact.
Injection molding is a manufacturing process for producing parts by injecting molten material into a mold. Injection molding can be performed with a host of materials mainly including metals (for which the process is called die-casting), glasses, elastomers, confections, and most commonly thermoplastic and thermosetting polymers.
Extrusion is a process used to create objects of a fixed cross-sectional profile. A material is pushed through a die of the desired cross-section.
Drawing is a similar process, which uses the tensile strength of the material to pull it through the die. This limits the amount of change which can be performed in one step, so it is limited to simpler shapes, and multiple stages are usually needed. Drawing is the main way to produce wire. Metal bars and tubes are also often drawn.
Example 27.7b
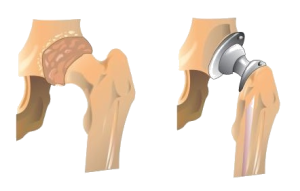
Example 27.7b source: Map: Chemistry for Changing Times (Hill and McCreary) by LibreTexts, licensed under CC BY-NC-SA 4.0.
Fiber Formation and Use
Nylon
Bill Pittendreigh, DuPont, and other individuals and corporations worked diligently during the first few months of World War II to find a way to replace Asian silk and hemp with nylon in parachutes. It was also used to make tires, tents, ropes, ponchos, and other military supplies. It was even used in the production of a high-grade paper for U.S. currency. At the outset of the war, cotton accounted for more than 80% of all fibers used and manufactured, and wool fibers accounted for nearly all of the rest. By August 1945, manufactured fibers had taken a market share of 25%. After the war, with the of shortages of both silk and nylon, nylon parachute material was sometimes repurposed to make dresses. Nylon fibers are used in carpet manufacturing, tire cord and in tires.
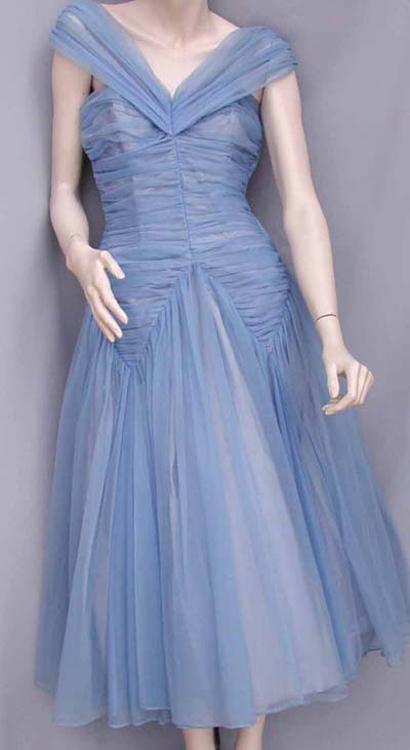
Polyester
Fabrics woven or knitted from polyester thread or yarn are used extensively in apparel (Figure 27.7d.) and home furnishings, from shirts and pants to jackets and hats, bed sheets, blankets, upholstered furniture and computer mouse mats. Polyester fabrics are highly stain resistant. Industrial polyester fibers, yarns and ropes are used in car tire reinforcements, fabrics for conveyor belts, safety belts, coated fabrics and plastic reinforcements with high-energy absorption. Polyester fiber is used as cushioning and insulating material in pillows, comforters and upholstery padding.
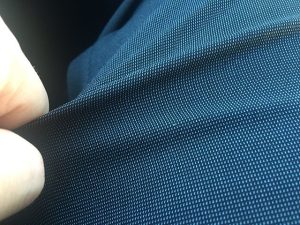
Acrylics
Acrylic fibers are synthetic fibers made from a polymer (polyacrylonitrile) with an average molecular weight of -100,000, about 1900 monomer units. For a fiber to be called “acrylic” in the US, the polymer must contain at least 85% acrylonitrile monomer. Typical comonomers are vinyl acetate or methyl acrylate. DuPont created the first acrylic fibers in 1941 and trademarked them under the name Orlon. It was first developed in the mid-1940s but was not produced in large quantities until the 1950s. Strong and warm, acrylic fiber is often used for sweaters and tracksuits and as linings for boots and gloves, as well as in furnishing fabrics and carpets. It is manufactured as a filament, then cut into short staple lengths similar to wool hairs, and spun into yarn.
Modacrylic is a modified acrylic fiber that contains at least 35% and at most 85% acrylonitrile monomer. The comonomers vinyl chloride, vinylidene chloride or vinyl bromide used in modacrylic give the fiber flame retardant properties. End-uses of modacrylic include faux fur, wigs, hair extensions and protective clothing.
Microfibers
Microfiber (or microfibre) is synthetic fiber finer than one denier or decitex/thread, having a diameter of less than ten micrometers. This is smaller than the diameter of a strand of silk (which is approximately one denier), which is itself about 1/5 the diameter of a human hair (Figure 27.7e.).
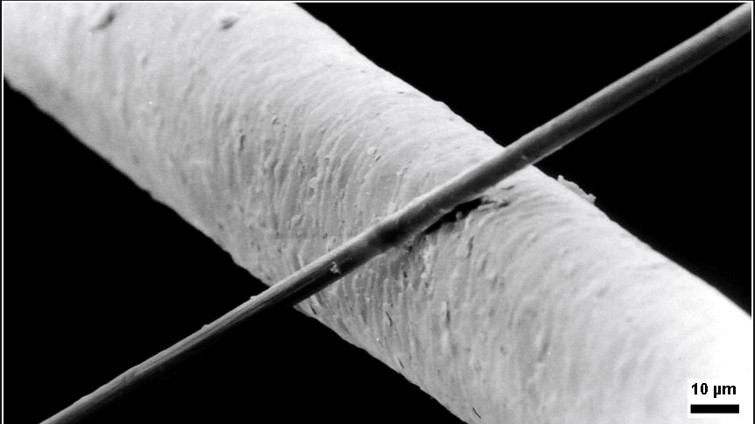
The most common types of microfibers are made from polyesters, polyamides (e.g., nylon, Kevlar, Nomex, trogamide), or a conjugation of polyester, polyamide, and polypropylene. Microfiber is used to make mats, knits, and weaves for apparel, upholstery, industrial filters, and cleaning products. The shape, size, and combinations of synthetic fibers are selected for specific characteristics, including softness, toughness, absorption, water repellency, electrostatics, and filtering capabilities.
Microfiber textiles tend to be flammable if manufactured from hydrocarbons (polyester) or carbohydrates (cellulose) and emit toxic gases when burning, more so if aromatic (PET, PS, ABS) or treated with halogenated flame retardants and azo dyes. Their polyester and nylon stock are made from petrochemicals, which are not a renewable resource and are not biodegradable. However, if made out of polypropylene, they are recyclable (Prolen).
For most cleaning applications they are designed for repeated use rather than being discarded after use. An exception to this is the precise cleaning of optical components where a wet cloth is drawn once across the object and must not be used again as the debris collected are now embedded in the cloth and may scratch the optical surface.
Microfiber products may also have the potential of entering the oceanic water supply and food chain similar to other microplastics. Synthetic clothing made of microfibers that are washed can release materials and travel to local wastewater treatment plants, contributing to plastic pollution in water. Fibers retained in wastewater treatment sludge (biosolids) that are land-applied can persist in soils. A study by the clothing brand Patagonia and University of California, Santa Barbara, found that when synthetic jackets made of microfibers are washed, on average 1.7 grams (0.060 oz) of microfibers are released from the washing machine. These microfibers then travel to local wastewater treatment plants, where up to 40% of them enter into rivers, lakes, and oceans where they contribute to the overall plastic pollution. Microfibers account for 85% of man-made debris found on shorelines worldwide.
No pesticides are used for producing synthetic fibers in comparison to cotton. If these products are made of polypropylene yarn, the yarn is dyed without any use of water compared to dying cotton, where thousands of liters of water become contaminated.
Attribution & References
Except where otherwise noted, this page has been adapted by Samantha Sullivan Sauer from
- “10.6: Properties of Polymers” and “10.3: Addition Polymerization” by Marisa Alviar-Agnew (Sacramento City College) In Map: Chemistry for Changing Times (Hill and McCreary) & LibreTexts, licensed under CC BY-NC-SA 4.0. Contributors from original source:
- Stephen Lower, Professor Emeritus (Simon Fraser U.) Chem1 Virtual Textbook (IF Figureis used), Marisa Alviar-Agnew (Sacramento City College)
- Wikipedia
- “10.3: Addition Polymerization” by Marisa Alviar-Agnew (Sacramento City College) In Map: Chemistry for Changing Times (Hill and McCreary) & LibreTexts, licensed under CC BY-NC-SA 4.0. Contributors from original source:
- Stephen Lower, Professor Emeritus (Simon Fraser U.) Chem1 Virtual Textbook, Charles Ophardt (Professor Emeritus, Elmhurst College); Virtual Chembook
- Wikipedia
- Beginning Chemistry (Ball), CC BY-NC-SA 3.0, a LibreTexts version of Beginning Chemistry (v 1.0).
- Basics of General, Organic, and Biological Chemistry (Ball et al.) by David W. Ball, John W. Hill, and Rhonda J. Scott via LibreTexts, CC BY-NC-SA 4.0./ A LibreTexts version of Introduction to Chemistry: GOB (v. 1.0), CC BY-NC 3.0.
Temperature where the thermal kinetic energy becomes high enough to allow internal rotation to occur within the bonds and to allow the individual molecules to slide independently of their neighbors
process of manufacturing by shaping liquid or pliable raw material using a rigid frame called a mold or matrix
forming process in which a plastic material is placed directly into a heated metal mold then is softened by the heat and therefore forced to conform to the shape of the mold, as the mold closes
manufacturing process where casting material is forced into a mold
manufacturing process for producing parts by injecting molten material into a mold
process used to create objects of a fixed cross-sectional profile
uses the tensile strength of the material to pull it through the die
synthetic fiber finer than one denier or decitex/thread, having a diameter of less than ten micrometers