27.2 Classification of Polymers
Learning Objectives
By the end of this section, you will be able to:
- Distinguish between thermoplastic and thermosetting polymers
- Distinguish between addition and condensation polymers
Polymers can be classified in two ways: based on their physical response to heating resulting in how they are used and based on their method of polymerization resulting from how they are prepared.
Plastics
The term plastics is used to describe polymers that are capable of being molded (formed into a shape) or are pliable. (Hein et al., 2014)
Thermoplastic and Thermosetting Polymers
Polymers are classified by their physical behaviour when heated. Thermoplastic polymers are soften when heated. They are plastics that become firm again when cooled. Thermoplastic polymers are common because the cycle of heating and cooling is common in the forming and recycling process and allows the polymer to be reformed. (Libretexts, 2022)
In thermoplastic polymers, monomer molecules are joined end to end in a linear chain with little to no cross linking between the chains. (Hein et al., 2014) In Figure 27.2a. and Figure 27.2b., the thermoplastic polymer (also called an elastomer in this image) shows multiple strands of polymer chains but no connection between any of the strands so the polymer can be stretched. Polyethylene is an example of a thermoplastic polymer. (Hein et al., 2014)
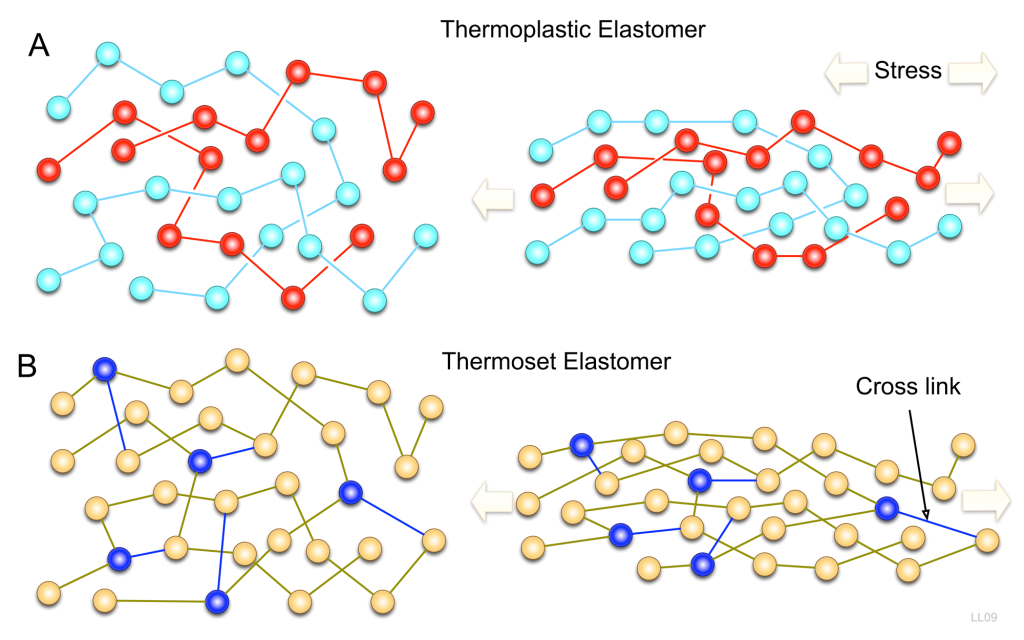
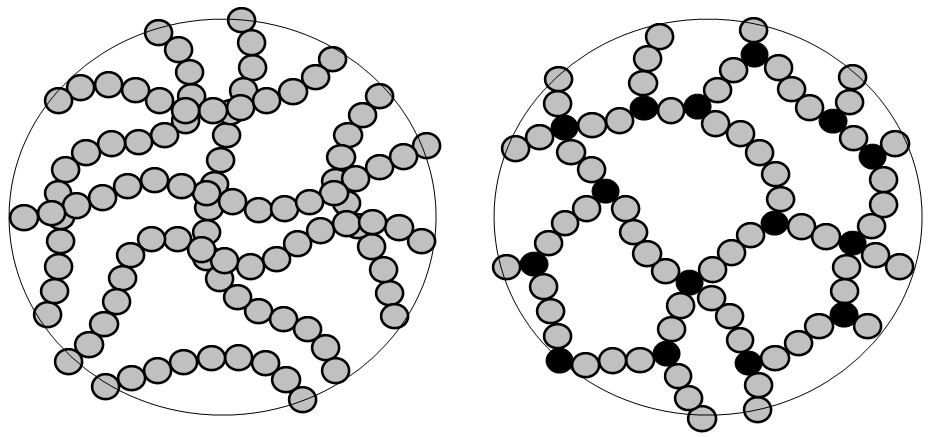
Thermosetting polymers soften when heated. They are plastics that can be molded but will harden permanently when cooled. If heated, thermosetting polymers will decompose. A common example is Bakelite commonly used in objects that require stiffness and some heat insensitivity such as toasters, pot handles, electrical components and billiard balls. (Libretexts, 2022) In a thermoplastic polymer, the polymer chains are cross linked resulting in an infusible solid.(Hein et al., 2014) Figure 27.2a. and 27.2b. show the structure of the polymer chains in a thermosetting polymer.
Addition and Condensation Polymers
Addition polymerization and condensation polymerization are two modes of polymerization reactions in the formation of polymers.
In an addition polymerization, the monomer molecules bond to each other without the loss of any other atoms. Addition or chain-growth polymerization involves the rearrangement of bonds within the monomer in such a way that the monomers link up directly with each other. Figure 27.2c. shows the formation of ethylene through addition polymerization. Addition polymers from alkene monomers or substituted alkene monomers are the biggest groups of polymers in this class. Ring opening polymerization can occur without the loss of any small molecules.
In condensation polymerization, two different monomers combine with the loss of a small molecule, usually water. Most polyesters and polyamides (nylon) are in this class of polymers. Figure 27.2d. shows the condensation polymerization of Nylon 6,6. A large number of important and useful polymeric materials are not formed by addition polymerization, but proceed instead by conventional functional group transformations of polyfunctional reactants. These polymerizations often (but not always) occur with loss of a small byproduct, such as water, and generally (but not always) combine two different components in an alternating structure.
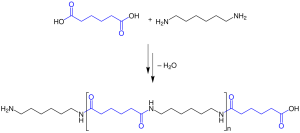
Attribution & References
Except where otherwise noted, this page has been adapted by Samantha Sullivan Sauer from:
- “10.3: Addition Polymerization – One + One + One + … Gives One!” In Map: Chemistry for Changing Times (Hill and McCreary) by LibreTexts, licensed under CC BY-NC-SA 4.0. Original attributions from source:
- Stephen Lower, Professor Emeritus (Simon Fraser U.) Chem1 Virtual Textbook
- Beginning Chemistry (Ball), CC BY-NC-SA 3.0, a LibreTexts version of Beginning Chemistry (v 1.0).
- Basics of General, Organic, and Biological Chemistry (Ball et al.)by David W. Ball, John W. Hill, and Rhonda J. Scott via LibreTexts, CC BY-NC-SA 4.0./ A LibreTexts version of Introduction to Chemistry: GOB (v. 1.0), CC BY-NC 3.0.
- Marisa Alviar-Agnew (Sacramento City College)
- Charles Ophardt (Professor Emeritus, Elmhurst College); Virtual Chembook
- Wikipedia
- “10.5: Condensation Polymers” In Map: Chemistry for Changing Times (Hill and McCreary) by Marisa Alviar-Agnew (Sacramento City College) & LibreTexts, licensed under CC BY-NC-SA 4.0. Original attributions from source:
- William Reusch, Professor Emeritus (Michigan State U.), Virtual Textbook of Organic Chemistry
- Stephen Lower, Professor Emeritus (Simon Fraser U.) Chem1 Virtual Textbook
- Marisa Alviar-Agnew (Sacramento City College)
- Jim Clark (Chemguide.co.uk)
- Wikipedia
polymers that are capable of being molded (formed into a shape) or are pliable
plastics that soften when heated and become firm again when cooled
plastics that soften when heated and can be molded, but harden permanently
monomer molecules bond to each other without the loss of any other atoms
two different monomers combine with the loss of a small molecule, usually water