Part 1: Power Plant Systems
Power Plant Systems
Boiler Feedwater Systems
Boiler feedwater systems include the equipment between the turbine condenser and the economizer of the boiler.
Modern designs are more complex as efficiencies are increased using:
-
- Bleed steam to heat feedwater
- Excess process steam to heat the feedwater.
Activity: Feedwater Systems
Click on the arrows to view different feedwater systems.
Utility Plant Feedwater Systems
Low pressure feedwater heaters
-
- Located between the extractions pumps and the deaerating heater.
- Deaerator heater is a low pressure heater
High pressure feedwater heaters
-
- Downstream of the boiler feedwater pumps and the boiler economizer.
Closed and Open Feedwater Heaters
Open Feedwater Heater:
- Direct-contact heat exchanger in which extracted steam is allowed to mix with the feedwater.
- A deaerator is a specifically designed open feedwater heater used to remove non-condensable gases from the feedwater.
Deaerators are considered open feedwater heaters.
-
- Serves two purposes:
- to heat the feedwater
- remove gases such as oxygen and carbon dioxide from the water.
- Serves two purposes:
The storage compartment of the deaerator also serves as a suction/storage tank for the boiler feedwater pump.
Video: Deaerator
Watch the video ” Dearator by Megatherm D’tech Pvt. Ltd.” [1:44]
The deaerator consists of two horizontal pressure vessels. . The top vessel is the deaerating heater while the bottom vessel is the storage compartment. The heater section accomplishes the heating and deaeration of the incoming water. Water flows into the inlet water box and then is distributed over the trays by the sprays. The water is broken down into small droplets, by spring loaded spray nozzles. Water cascades down the trays, and coming into intimate contact with steam.
Deaerators
Typical operating parameters for a pressurized deaerator:
-
- The operating pressure will usually be approximately 0.2 bar (3 psi), which gives a saturation temperature of 105°C (221°F).
- Contains between 10 and 20 minutes water storage for the boiler on full-load.

Gas removal from water depends upon three factors:
-
- Whether the gas ionizes in the water or is dissolved as a free gas.
- Oxygen is a free gas and easily removed
- Carbon Dioxide and Ammonia ionize in the water and are difficult to remove
- The relative pressures of the gas in the water and in the atmosphere.
- The water temperature.
- Whether the gas ionizes in the water or is dissolved as a free gas.
Deaerators can be Atmospheric or Pressurized.
Activity: Steps of Atmospheric Deaeration
Click through the tabs to learn about the steps of Atmospheric Deaeration.
Activity: Images of Deaerators
Click the arrows to view images of Deaerators.
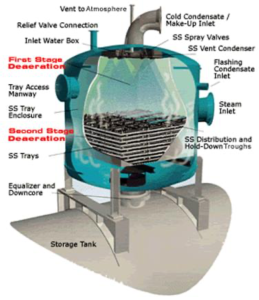
Mechanical Deaeration
Dissolved gases are removed by:
-
-
- Raising the water temperature to the boiling point causing gases to be released to the atmosphere.
- The bulk of the oxygen and gases are removed in the spray section above the trays.
- The water is also scrubbed with a flow of steam to sweep away the released gases.
- Only 5% of the oxygen is removed in the final polishing tray section.
- Oxygen level must be down to 5-7 parts per billion in the deaerator effluent.
- Raising the water temperature to the boiling point causing gases to be released to the atmosphere.
-
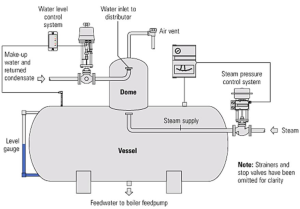
- Deaerator supervisory equipment?
- Relief Valves
- Pressure Gauge
- Thermometer
- Control Valves
- Level Switches
- Overflow Valves
- Gauge Glass

Deaerator Cost and Justification
Cost
-
-
- No additional energy cost associated with operating a deaerator
- Steam used to increase the feedwater temperature is compensated by higher boiler output.
- Some heat loss from the deaerator.
- Additional cost of running the transfer pump between the feedtank and the deaerator.
- Some steam is lost with the vented non-condensable gases.
- No additional energy cost associated with operating a deaerator
-
Justification
-
-
-
- The principle reasons for selecting a pressurized deaerator are:
- To reduce oxygen levels to a minimum without the use of chemicals.
- A cost saving with respect to chemicals
- Blowdown rate will be reduced with associated cost savings.
- The principle reasons for selecting a pressurized deaerator are:
-
-
Feedwater Heater Operation
Closed feedwater heaters have a level controller to keep the condensate at the desired level.
-
-
- The heaters usually are set up to trip off and bypass if the condensate level becomes too high — i.e. tube leak.
- Feedwater heaters may be taken off line and bypassed for maintenance or to generate more power on a short term basis.
-