Part 2: Instrumentation and Control Systems
Feedwater Control Systems
Rapid response from the feedwater flow control is necessary and becomes progressively more acute as boiler size and pressure increase.
Thermostatic Expansion Regulator
Thermostatic Expansion Regulators utilize an inclined tube within a tube, which is connected between the feedwater control valve and the boiler. The inner tube is linked to both the steam space and the water space inside the boiler. When the water level in the boiler indicates a low level, the inner tube heats up as a result of the increased steam space at the lower level, subsequently heating the outer tube. This causes the water inside the outer tube to increase in pressure, and it acts on the feedwater valve, causing it to open. Conversely, the opposite occurs when the boiler experiences high water level conditions.
Activity: Thermal Expansion Regulator
Click the arrows to learn more about thermal expansion regulators.
Single-Element Control Systems
Within a transmitter, a diaphragm is utilized to separate two sides. On one side, a constant head of water is maintained, while the other side is exposed to the varying head resulting from changes in the drum level within the boiler. This control mechanism is referred to as feedback control since it responds solely to alterations in the boiler water level, enabling precise level regulation.
Activity: Single-Element Feedwater Control
Click the arrows to learn more about single-element feedwater controls.
Single-element feedwater control systems are satisfactory for small base-loaded heating boilers but not suitable for boilers that operate with higher flows, changing loads, or higher pressures.
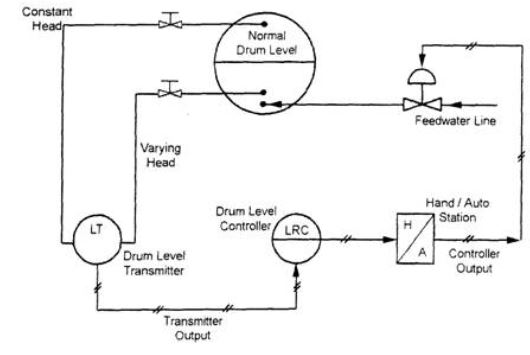
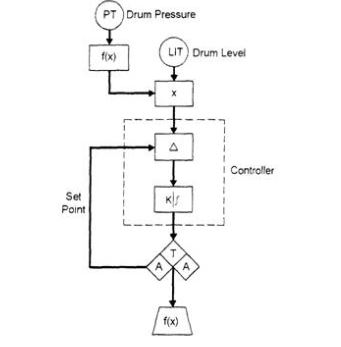
Two-Element Feedwater Control
Two-element feedwater control is utilized to compensate for drum level changes caused by varying steaming rates, unlike single-element control. During periods of rapid steaming, steam bubbles can occupy a considerable volume of the available water space in the drum, often accounting for upwards of 35%. The two-element control system effectively manages these steam bubble fluctuations and maintains a stable water level in the drum.
Swell
A rapid increase in boiler load leads to several interconnected consequences.
- An immediate increase in steam flow from the boiler.
- A sudden drop in boiler steam drum pressure.
- A corresponding drop in the boiling temperature of the water, and the heat energy, already in the water, converts a larger volume of water into steam.
Increased volume of steam bubbles in the drum and water walls causes a rise in the drum level.
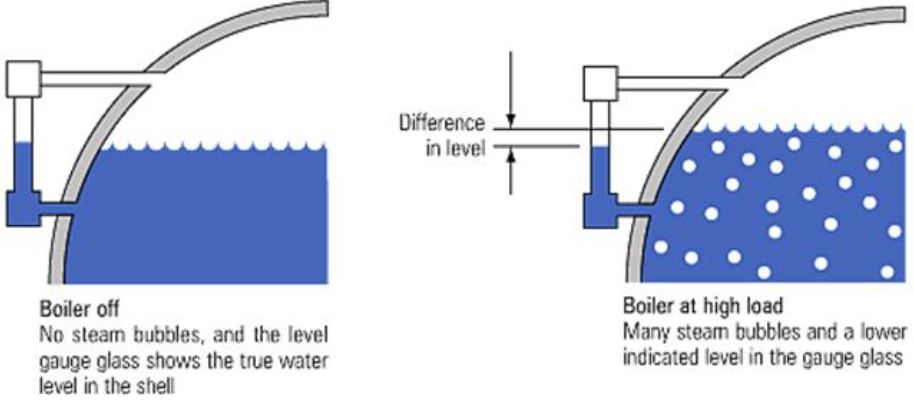
When there is a rapid increase in boiler load, there are:
- An increase in combustion rate to bring the boiler pressure back to normal.
- An increase in the volume of steam in the boiler water space, which causes the drum level to rise.
Shrinkage
Shrinkage refers to the phenomenon where a decrease in the boiler firing rate triggers a series of effects in the system. Initially, the decrease in firing rate causes the drum pressure to increase, leading to a rise in the boiling point of the water inside the boiler. As a consequence of this, the vapor-water ratio in the waterwalls is reduced, resulting in the collapse of steam bubbles in both the drum and waterwalls. This collapse causes a decrease in the drum level. To compensate for this drop in level, the single-element control system responds by increasing the feedwater flow to the boiler drum, aiming to restore and stabilize the water level.
These water level changes on the single-element feedwater controller cause it to make exactly the opposite adjustments to those that are actually required. An increased load requires increased feedwater flow, but the high water level resulting from swell causes the single-element controller to reduce the flow. The initial incorrect movement makes water level control more erratic at times of rapidly changing boiler load and increases the recovery time.
Two-Element Feedwater Control measures the drum water level and steam flow. It uses these measurements to set the required feedwater flow. The steam flow signal is used as a feedforward signal for the drum level.

Activity: Two-Element Feedwater Control
Click the arrow to learn more about two-element feedwater control.
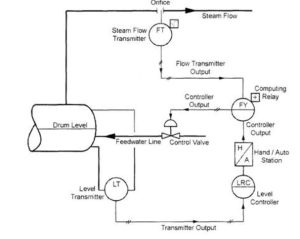
When the boiler load decreases, a process similar to what occurs during a load increase takes place. The decrease in load causes the steam flow to become dominant and overrides the drum level’s response to shrinkage until the drum level returns to its normal operating range. This mechanism helps to stabilize the boiler system and maintain the desired water level even during fluctuating load conditions.
Two-Element Feedwater Control is implemented using a proportional-plus-integral controller and is highly effective in managing the boiler drum level. It works to bring the level back to the setpoint once the effects of swell or shrinkage have been mitigated. This control strategy can also be referred to as a feedforward system since it anticipates the impact of load changes on the drum level and proactively adjusts the feedwater flow to prevent significant fluctuations in the water level.
Three-Element Feedwater Control
Three-Element Feedwater Control takes into account the principle that every kilogram of feedwater entering the boiler is converted into a kilogram of steam at the boiler outlet through evaporation. In addition to the two elements – drum level and steam flow, the third element used in this control system is feedwater flow. This inclusion of feedwater flow allows the control system to effectively address and overcome the effects of both swell and shrinkage, ensuring precise and responsive regulation of the boiler drum level while considering the variations in the feedwater flow rate.
Activity: Three-Element Control
Click the image hotspot to learn more about three-element control.
Use the slider to learn about the three-element feedwater control system.
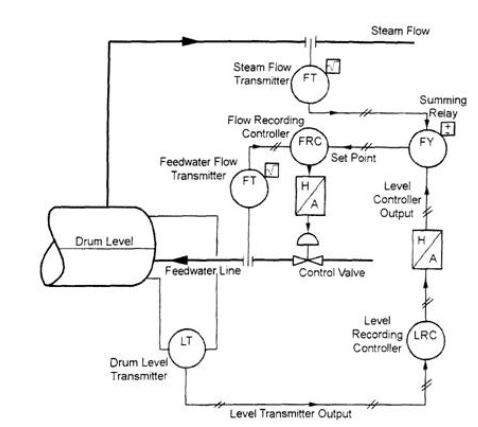
Large steam generators may use a separate, smaller feedwater control valve with a single-element control scheme, for startups and very low loads. Alternatively, there may be a single feedwater control valve, or bank of valves, controlled from one controller that can be transferred between single-element and three-element control. In some cases, this transfer is made automatically as the load is increased or decreased past a predetermined transfer point.
If the correct drum level is not maintained, due to a condition such as intermittent boiler blowdown, the relationship between the steam flow and the water flow is changed automatically by the level controller to maintain the proper drum level. The drum-level transmitter helps make this correction.
In this type of control, the drum level transmitter output is compared with the level setpoint in the LRC. The output of the level controller is compared with the steam flow transmitter output at the summing relay. The output of the summing relay then becomes the setpoint signal for the feedwater flow-recording controller (FRC).
An increase in steam flow increases the setpoint signal to the feedwater flow-recording controller and opens the feedwater control valve further. Since this is a proportional–plus–reset controller, it keeps increasing the water flow until the output of the water flow transmitter is equal to the setpoint signal. This overcomes the influence of the drum level transmitter and controller which is under the effect of swell. As the swell subsides, the drum level transmitter and controller bring the drum level back to the set point.
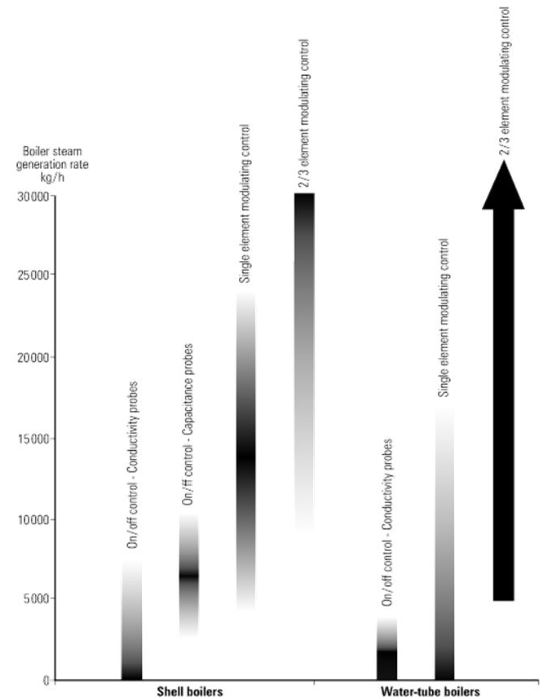