Part 3
Steam Temperature Control
Considerations for superheated steam temperature when used to drive a turbine:
- Turbines are designed to operate most efficiently under set temperature conditions.
- Steam temperature changes cause differential expansion or contraction between the turbine rotor and the turbine casing.
- An excessive rise in steam temperature weakens the metals used in both the superheater and the turbine.
- An excessive drop in steam temperature causes condensation in the low-pressure stages, causing blade erosion and loss of efficiency.
The purpose of steam temperature control is to maintain the same final steam temperature at both high and low loads. Basic control is usually achieved by arranging a balance between the radiant and convection superheater sections in the boiler design.
Final steam temperature control methods:
- Attemperation (desuperheating)
- Gas bypass
- Gas recirculation
- Tilting burners
Attemperation (Desuperheating)
Activity: Three-Element Attemperator
Click the image slider to learn more about three-element attemperators.
Two-element control:
Steam Flow: the initial adjustment is done by measuring steam flow and sending a signal to the final control based on that variable.
Final Steam Temperature: the final adjustment, or trim, is achieved by monitoring the final steam pressure.
Three-element control
Three signals are received by the attemperator regulating valve relay, from:
- Flowmeter: steam flow.
- Thermal element: located after the attemperator spray nozzle and before the second-stage superheater.
- Thermal element: located after the second-stage superheater, steam outlet temperature.
Turndown ratio
The turndown ratio is a range of flow rates over which the desuperheater will operate.
Two turndown values may be specified for a particular desuperheater:
- Steam turndown ratio: a range of steam flow rates that the device can effectively desuperheat.
- Cooling water turndown ratio: a range of cooling flow rates that can be used.
Two types of attemperators (desuperheaters) are used:
- Surface type: the cooling medium is separated from the steam by a tube surface (shell and tube design).
- Direct Contact type: the cooling medium is mixed and comes in direct contact with the steam. Feedwater or demineralized water is sprayed directly into the steam.
Shell Attemperator
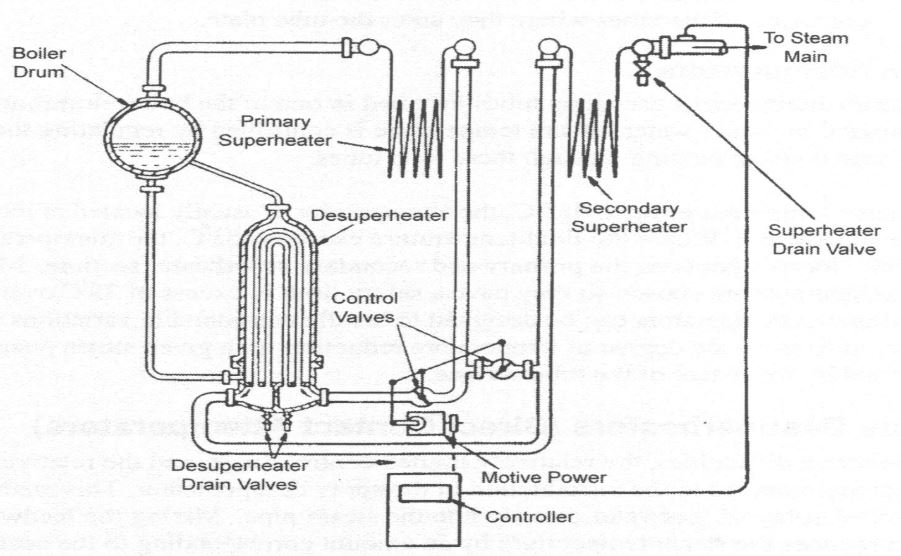
Shell attemperators consist of a shell containing an inverted U-shaped nest of tubes expanded into a tube plate. The shell and tube plate are connected to a forged steel base which forms part of the steam pipe. Control valves, which are mechanically linked, regulate the amount of steam that can be passed through the tube nest. The space between the tubes and the shell is filled with water at saturation temperature (supplied by the boiler drum). Steam passing through the tube nest is cooled before being mixed again with steam at the entry to the next stage of superheating. The extent of opening of the control valves and, as a result, the quantity of steam passing through the tube nest, governs the amount of desuperheating applied to the steam.
Disadvantages:
- The difference in temperature between the inside of the shell and the live steam in the base makes it difficult to maintain a tight joint between the two sections.
- Chemically treated water in the boiler drum can pass into the shell and is extremely difficult to blow down.
- Settlement at the bottom of the shell leads to corrosion of the tubes where they enter the tube plate.
Condenser Attemperators
Condenser Attemperators are loop tubes installed in the superheater inlet header. Feedwater passes through these loop tubes and partly condenses the steam passing through the superheater inlet header and around the loop pipes.
Advantages:
- The turndown is only limited by the controls that are fitted.
- This design is capable of producing desuperheated steam to within 5°C of the saturation temperature.
- High maximum operating temperatures and pressures, typically around 60 bar and 450°C.
- Fast response.
Disadvantages:
- Bulky, because there are now a number of in-line devices available, they have been largely superseded.
- High cost.
Drum-Type
The drum-type attemperator are surface attemperators, they make use of loop tubes installed within one of the boiler drums and surrounded by boiler water. Regulating the amount of superheated steam that passes through these loop tubes controls steam temperature.
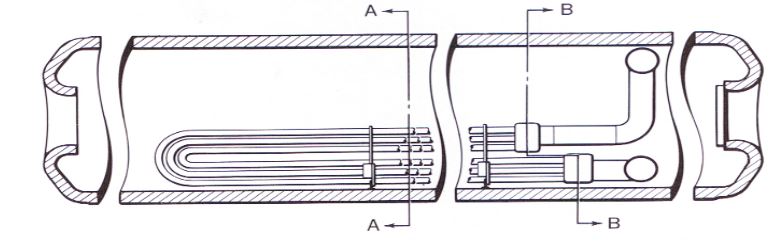
Direct Contact Attemperator
Direct contact attemperator is a steam conditioning system where water is injected directly into the steam flow to control its temperature.
Activity: Direct Contact Attemperator
Click the image hotspots to learn how direct contact attemperators work.
Venturi Desuperheaters
Venturi desuperheaters are devices used to reduce the temperature of steam or gas by mixing it with water in a venturi-shaped nozzle. Desuperheating is carried out in two stages:
- First stage: in the internal diffuser, a portion of the steam is accelerated in the internal nozzle, and the velocity is used to atomize the incoming water.
- Second stage: saturated mist or fog emerges from the internal diffuser into the main diffuser where it mixes with the remainder of the steam.
Advantages:
- Steam turndown ratios of up to 5:1 and cooling water turndowns of over 20:1.
- Simple operating principle.
- No moving parts.
- Accurate control of steam temperature; typically within 3°C of the saturation temperature.
- Suitable for operation under steady or variable steam conditions.
- There is reduced wear in the downstream pipework compared to a spray-type desuperheater, as the cooling water emerges as a mist rather than as a spray.
Disadvantages:
- Pressure drop is incurred (although this is generally small and within acceptable limits).
- The absorption length is still longer than the steam atomizing type; so more space is required for installation.
- A minimum cooling water flow rate is required.
Single-Stage Desuperheater
A single-stage desuperheater is a steam conditioning device that reduces the temperature of superheated steam in a single step by injecting water into the steam flow.
Advantages:
- Simple in operation.
- Cost-effective.
- Minimum steam pressure drop.
Disadvantages:
- Low turndown ratio, typically a maximum of 3:1 on both steam and cooling water flow.
- Desuperheated steam temperature can only be reduced to 10°C above the saturation temperature.
- Longer absorption length than the steam atomizing type.
- Most prone to cause erosion damage to the internal pipework. This can be overcome by the use of a thermal sleeve.
- Limited pipe sizes.
Two-Stage Desuperheater
Two-stage desuperheaters are used where there are three sections of the superheater. One nozzle is located between the first and second superheat sections and another between the second and third sections. Each nozzle has its own control valve which is operated sequentially.
Spray Desuperheaters
Spray desuperheaters are affected by the following factors:
- Particle size: the smaller the water particle size, the greater the ratio of surface area to mass, and the higher the rates of heat transfer.
- Cooling water flow rate: the rate at which cooling water can be added to the superheater steam.
- Turbulence: as the flow within the pipeline becomes more turbulent, the individual entrained water particles reside longer in the desuperheater, allowing for greater heat transfer.
Gas Bypass
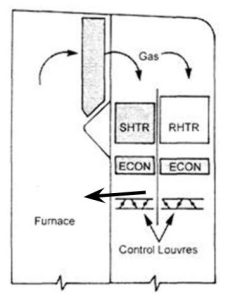
Gas bypass refers to the process of diverting a portion of the gas turbine’s exhaust gases away from the main flow to control the temperature and pressure levels during off-design operating conditions.
Activity: Gas Bypass
Click the image hotspot to learn more about gas bypass.
Disadvantages:
- Difficult to maintain dampers in proper operating condition due to the high temperatures they are exposed to.
- Response to temperature changes is somewhat sluggish.
Gas Recirculation
Activity: Gas Recirculation
Click the notches to learn more about gas recirculation.
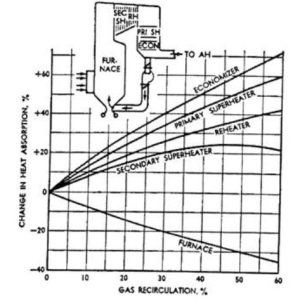
Tilting Burners
Tilting burners, also called movable burners alter the burner angle by raising or lowering the main body of the furnace fireball. It also alters the proportion of the heat released between the radiant and convection sections of the superheater.
Activity: Tilting Burner
Scroll through the information wall to learn about the effects of tilting a burner.