4.5 Hazard Control
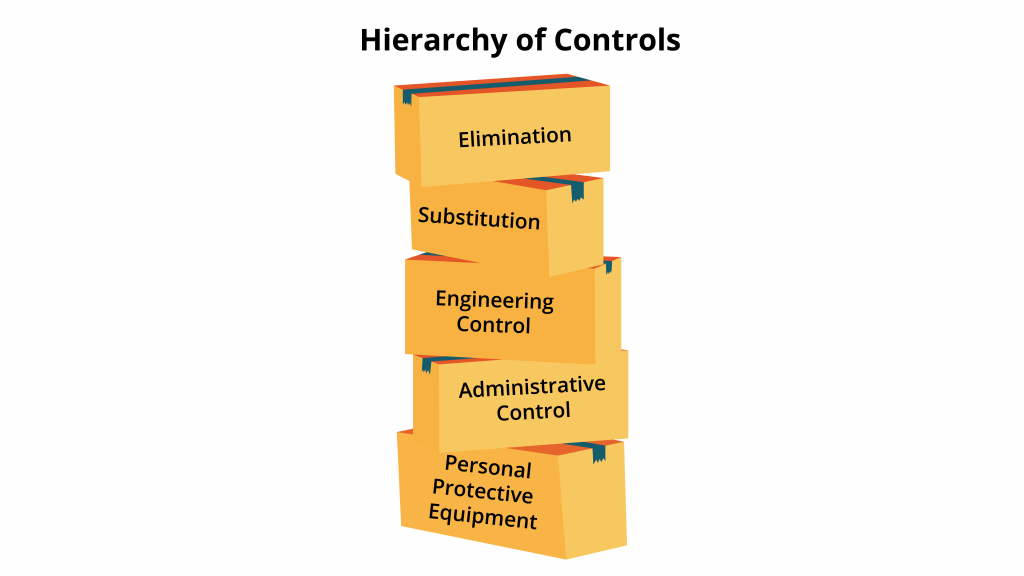
The final step in the HRAC process is to determine and implement the most appropriate control for each hazard. Hazard control is a regulatory requirement in every Canadian jurisdiction and entails implementing measures to eliminate or reduce the potential of a hazard causing an incident. Employers must exercise due diligence in the HRAC process in order to avoid prosecution for any workplace injuries under OHS law. Some forms of hazard control are more effective than others, and, consequently, a hierarchy of controls (with five levels) has been established:
- Elimination removes the hazard from the worksite. For example, relocating work performed at a height to ground level eliminates the risk of falling. This control is most easily implemented at the design stage, thereby preventing the hazard from entering the workplace.
- Substitution entails replacing something that produces a hazard with something that does not. For example, we might replace chemical-based cleaning solvents with plant oil–based solvents. Substitution is similar to elimination but is less effective because the new object or process may introduce different hazards or fail to completely remove the original hazard.
- Engineering controls are modifications to the workplace, equipment, materials, or work processes that reduce workers’ exposure to hazards. For example, installing guards on machinery, building guard rails, installing ventilation systems, or purchasing ergonomically designed workstations all isolate workers from hazards, but they do not eliminate the hazard. These controls can be incomplete, become inoperative due to lack of maintenance, or be overridden and therefore are less effective than elimination or substitution.
- Administrative controls are changes to work process, policies, training, or rules designed to reduce exposure to hazards. For example, policies restricting the time workers spend in contact with a chemical hazard, “no-go” zones that restrict workers’ movements in certain locations, mandatory training sessions, permit systems to control access to equipment or spaces, changes to schedules to prevent excessive shift work, or working-alone procedures that require regular check-in are all administrative controls. Administrative controls do not actually control a hazard. Rather, they attempt (via rules and processes) to limit workers’ exposure to the hazard.
- Personal protective equipment (PPE) is equipment worn by workers that is designed to protect them should they come into contact with a hazard. For example, helmets, goggles, gloves, and fall protection systems are forms of PPE. PPE is considered the least effective control because it does not control the hazard or restrict workers’ contact with the hazard and is heavily reliant upon human action for its effectiveness. PPE places the burden of implementation on the worker. Workers may choose not to wear or be pressured into not wearing the PPE.
Multiple controls can be combined to provide a higher degree of control. Different levels of control may be appropriate at different times. For example, when first addressing a hazard it may be necessary to use PPE until a more permanent engineering control can be implemented. It is important to not unduly delay the implementation of the (likely more effective) engineering control. Employers have flexibility in how they control hazards, but that flexibility should not be interpreted as permission to disregard their due-diligence obligation to implement the most effective hazard control.
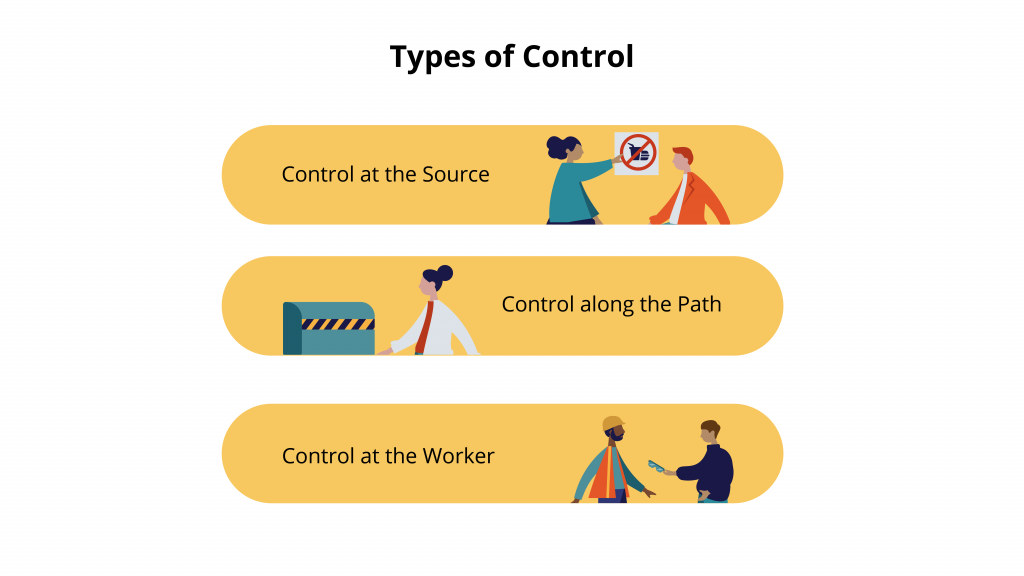
A more worker-centered approach is to consider the location of the control. In this approach, the focus is on where and when the hazard is controlled in the context of where the worker is in the production process. In this approach, hazards can be controlled at three locations:
- Control at the source addresses the hazard where it first occurs. This type of control prevents the hazard from entering the workplace via elimination, substitution, or some types of engineering controls.
- Control along the path addresses the hazard at some point between its source and when workers encounter the hazard (i.e., it prevents the hazard from reaching the worker). Some types of engineering controls (e.g., machine guards, local ventilation) control the hazard along the path.
- Control at the worker implements controls over the hazard only after it reaches the worker. These controls are designed to prevent or reduce the consequences of the hazard, rather than control the hazard itself. PPE and administrative controls are both examples of control at the worker because they both require that the burden of the control be placed almost exclusively upon the worker.
Examining controls by considering their location relative to the worker changes how we assess whether a control is effective by emphasizing the burden placed on workers with each control option. Note how the effectiveness of the control increases as the control moves closer to the source of the hazard.
The location approach allows for a more nuanced understanding of how different groups of workers can be differentially affected by a hazard. When attention is turned to the worker, rather than the hazard, differences between workers become more evident. For example, administrative controls are less effective for new workers, because they are less familiar with the rules and have not yet developed the skills required to work safely. Looking at how those administrative controls are located relative to the worker makes it more likely that their shortcomings for new workers will be identified. Similarly, the location approach draws more attention to the consequence of control failure and emphasizes the harm that can occur to workers when the system fails.
“Hazard Recognition, Assessment, and Control” in Health and Safety in Canadian Workplaces by Jason Foster and Bob Barneston, published by AU Press is licensed under a Creative Commons Attribution-NonCommercial-ShareAlike 4.0 International License, unless otherwise noted.