4.1 Identifying Physical Hazards
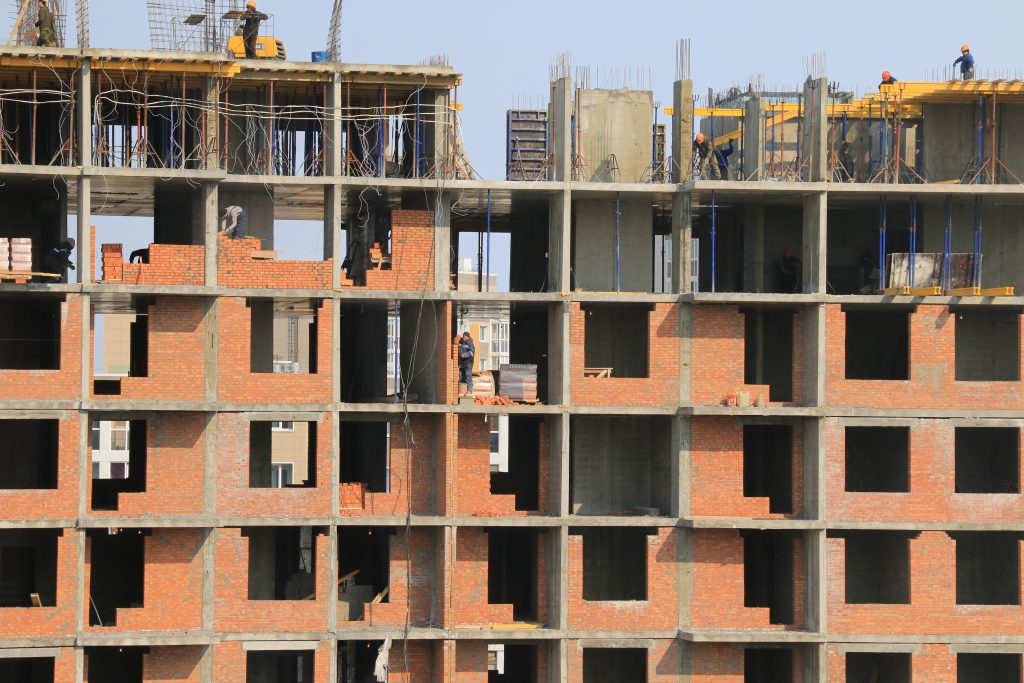
Story: Physical Hazards
On Christmas Eve, 2009, six employees of Metron Construction were repairing balconies at a Toronto high-rise apartment. All the men were newcomers to Canada, hailing from Latvia, Uzbekistan, and Ukraine. They were on a swing-stage scaffolding (the type of suspended scaffolding you often see on the outside of tall buildings) working on a 13th- floor balcony. Their project manager, Vadim Kazenelson, was on the balcony handing them tools. As Shohruh Tojiddinov, one of the workers on the scaffolding, later reported, Kazenelson decided to climb on to the scaffolding. “He said ‘where is the lifeline’ and [the site supervisor Fayzullo] Fazilov said ‘don’t worry’. . . .[Kazenelson] jumped onto the stage and the stage broke.” Tojiddinov was wearing a harness and when the stage broke he was left hanging in mid-air. “I looked up and I saw Vadim pulling me up. . . . I saw four deaths and one was still alive. I vomited.”[1]
As Kazenelson landed on the scaffolding, it split in two. Kazenelson was able to scramble back onto the balcony. The other five men fell to the ground, instantly killing four (Alesandrs Bondarevs, Aleksey Blumberg, Vladamir Korostin, and Fazilov). The fifth, Dilshod Marupov, was left permanently disabled. The scaffolding had only two lifelines available for the seven men and Tojiddinov was the only one using the fall protection. The scaffolding had been provided to Metron by Swing N Scaff Inc., a scaffolding supply company.
The investigation that followed the incident revealed that the scaffold was faulty and had not been designed or inspected properly by Swing N Scaff. It also found that the men, whose knowledge of English was limited, were not provided with any training about working at heights or using fall protection.[2] There was insufficient fall protection gear available to secure all the men. Subsequently, Kazenelson attempted to cover up the incident. He told Tojiddinov to say that Kazenelson had been on the ground and he gave him a safety manual on fall protection (in English, which Tojiddinov could not read), instructing him to say he had received it before the incident. [3]
This incident dramatically demonstrates what can happen when an employer fails to protect their workers from physical hazards. In this case, the employer failed to provide the workers with safety training and equipment to protect them from the primary hazard (falling from a height). The danger of the hazard was compounded by the workers’ limited ability to enforce their safety rights due to their limited language skills, minimal knowledge of health and safety laws, and weak negotiating position as new Canadians.
A hazard (which is sometimes called an agent) is anything that might harm, damage, or adversely affect any person or thing under certain conditions at work. It can be an object, process, context, person, or set of circumstances that has the potential to create negative health and safety outcomes. In this chapter, we will focus our attention on physical hazards. A physical hazard typically (but not always) entails a transfer of energy that results in an injury, such as box falling off a shelf and hitting a worker or a worker falling from a scaffold and hitting the ground.
Physical hazards are the most widely recognized hazards and include contact with equipment or other objects, working at heights, and slipping. This category also includes noise, vibration, temperature, electricity, atmospheric conditions, and radiation. More recently, OHS practitioners have also included the design of work and the workplace as physical hazards, suggesting it is important to attend to the ergonomic effects of work. This chapter discusses how to identify physical hazards and to determine ways to control some of the more common physical hazards. In discussing physical hazards, it is important to keep in mind that non-traditional work relations, such as the one highlighted in the opening vignette, can compound the risk associated with a physical hazard. We discuss the health and safety implications of non-traditional work relations more fully in the book.
Identifying Physical Hazards
In 2012, 50% of all WCB time-loss injuries in Canada were caused by physical hazards. Injuries caused by contact with an object/machine or falls was the most common type of injury.[4] Injuries caused by physical hazards are both overrepresented and underestimated in mainstream OHS. As we saw in Chapter 1, physical hazards are overrepresented in media portrayals of workplace incidents because they conform to commonly held views of safety hazards.[5] Hazards such as a slippery floor or an unguarded saw blade are easy to imagine and their effects on workers’ health are clear and direct.
At the same time, employers often underestimate the prevalence of (and thus fail to control) physical hazards. For example, an extension cord lying across a hallway floor is often seen as no big deal because it is a readily apparent and easily understood tripping hazard that we expect workers to avoid as a matter of course (“pick up your feet!”). When such hazards result in an injury, we often blame the worker for her inattention to the hazard rather than examine why the hazard was present and why the hazard was not controlled. The loose extension cord, for example, could have been eliminated as a hazard by re-running the wiring through the ceiling or moving the powered device closer to the plug in.
This example is a reminder that the definition of cause affects decisions about injury control. If worker carelessness or inattention is deemed to be the cause of an incident, then the controls will focus on correcting the worker rather than removing the hazard. Indeed, often the nature of physical hazards lends itself to devising “simple” solutions designed to alter worker behaviour rather than controlling the hazard itself. For example, the contact hazard posed by a doorway with unusually low clearance may be addressed by posting a sign saying “caution: low doorway” and expecting workers to duck as they pass through it. A more effective (but costlier) solution is to increase the doorway’s height.
Physical hazards also sometimes hide in plain sight. Often a hazard is so pervasive or workers’ behaviours to avoid the hazard are so routinized that the hazard is rendered almost invisible. For example, workers in a kitchen may use a dishtowel when opening an oven door to prevent the hot handle from burning them. Habitually turning a dishtowel into PPE prevents the injury and renders the hazard invisible. When identifying physical hazards, it is important to adopt the outlook of someone new to the workplace to bring back into view any hazards that have become invisible over time.
Prevention of Slips, Trips and Falls
What is the most effective way to prevent slips, trips, and falls in the workplace? This is an important question. In 2012, 18% of all Canadian lost-time claims involved a worker falling, either from a height or on the same level.[6] This figure significantly underrepresents the total number of incidents, as many slips and trips do not result in injury requiring time off work.
Most studies of trips and falls focus on factors related to workers, such as what caused workers to lose their balance, workers’ demographic characteristics, or whether workers followed safety principles they were taught in training.[7] Despite many such studies, most injury prevention efforts have been ineffective at reducing the incidence of slip, trips, and falls.[8] This may indicate that these studies are focused on the wrong issues.
In a recent analysis, Tim Bentley argues that the study of slips, trips, and falls has been focused too narrowly on what he calls the “active failures” that lead to incidents. Active failures are the immediate factors that lead to risk of injury, including individual factors connected to the time and place of the event such as demographics, perception, use of equipment, and the exposure to the hazardous situation.
Bentley calls for greater emphasis on latent failures, which are the “conditions that elicit substandard or unsafe behaviours that are present in the system without causing immediate threats but have the potential of being a step in an injury event.”[9] These include factors such as workplace design, the organization of work, management decisions, and environmental conditions such as climate. He argues that the perceptions and decisions made at the moment of active failure are shaped and bounded by existing latent failures.
The core of Bentley’s argument is that it is easy to look at who the worker was (e.g., a new worker) and what they were doing at the moment of the fall (e.g., not paying attention). As a result, most injury prevention efforts are focused on the worker. Bentley argues that employers should be focusing on the latent features of the incident— the pace of work, the design of the workplace, stress levels, and other systemic factors—that are more important in determining when a trip of fall will occur.
Bentley’s approach is similar to the notion of proximate and root cause. Essentially, injury prevention is more effective if we look beyond the obvious causes to see the underlying causal factors. This more holistic approach is supported by studies that suggest the most effective method for preventing slips, trips, and falls is to adopt a multi-faceted approach that includes enhanced hazard assessment, preventive design changes, training, management leadership, and greater attention to environmental factors.[10]
- Mehta, D. (2015, January 27). Manager didn’t insist on lifelines, court hears; Scaffold collapse. National Post, p. A8. ↵
- Wetselaar, S. (2014, December 4). Company fined after Christmas Eve scaffolding tragedy that killed four. Toronto Star. ↵
- CBC News. (2015, June 26). Vadim Kazenelson found guilty in deadly Toronto scaffolding collapse. CBC News Website, http://www.cbc.ca/news/canada/toronto/vadim-kazenelson-found-guilty-in-deadly-toronto-scaffolding-collapse-1.3128868 ↵
- AWCBC. (2014). National work injury, disease and fatality statistics 2010–2012. Ottawa: Association of Workers’ Compensation Boards of Canada. ↵
- Barnetson, B., & Foster, J. (2015). If it bleeds it leads. ↵
- AWCBC. (2014). ↵
- Hsiaoa, H., & Simeonova, P. (2001). Preventing falls from roofs: A critical review. Ergonomics, 44(5), 537–561; Kemmlert, K., & Lundholm, L. (2001). Slips, trips and falls in different work groups—with reference to age and from a preventive perspective. Applied Ergonomics, 32(2): 149–153; Lipscomb, H., Dale, A. M., Kaskutas, V., Sherman-Voellinger, R., & Evanoff, B. (2008). Challenges in residential fall prevention: Insight from apprentice carpenters. American Journal of Industrial Medicine, 51(1), 60–68. ↵
- Rivara, F., & Thompson, D. (2000). Prevention of falls in the construction industry: Evidence for program effectiveness. American Journal of Preventive Medicine, 18(4), 23–26. ↵
- Bentley, T. (2009). The role of latent and active failures in workplace slips, trips and falls: An information processing approach. Applied Ergonomics, 40, 177. ↵
- Bell, J., et al. (2008). Evaluation of a comprehensive slip, trip and fall prevention programme for hospital employees. Ergonomics, 51(12), 1906–1925. ↵
is anything that might harm, damage, or adversely affect any person or thing under certain conditions at work.
Workplace hazards potentially giving rise to injuries typically (but not always) caused by a transfer of energy that result in an injury.