5.3 – Selection and troubleshooting motors
How to select a motor
First, you will need to collect information on the type of application and the purpose you are trying to achieve with the motor. You can do this by asking a series of questions such as:
- How much is the load? How many RPMs do you need?
- Do you actually need a motor or a pump?
- For example, in dialysis machines they use brushless DC gear motors to move the dialysate, peristaltic pumps to move the blood and diaphragm pumps to meter the acid concentrate, sodium bicarbonate and ultrafiltration fluids.
Once you have decided on the purpose, you can design the electronics circuit accordingly: AC or DC
How to choose a stepper motor for biomedical equipment
When selecting a stepper motor for a medical device, you will need to consider many factors. For example, a systolic pump may require accuracy in a small package while lab devices (ex: blood sampler) may need to be very quiet. Regardless of the type of motor you require, there are always some things that you should consider:
Size
Size
Stepper manufacturers adhere to NEMA standards (industry standards governing motor size), step motors range from NEMA-8 to NEMA-42. For medical applications, space constraints are often critical. Generally: the smaller the motor, the better. Smaller motors also need less power, so they save energy. However a drawback to smaller motors is they provide less torque. Remember, smaller does not mean less expensive, building small and precise motors costs more. Finally, length is often critical for fitting the motor into medical devices. NEMA standards do not account for length and length can vary among motor manufacturers
Accuracy
Accuracy
Stepper motors can step in increments of 1.8°, 0.9° or even 0.45°. Motors can also be microstepped: 64× microstepping a motor divides the 0.9° into steps of 0.014°. • All step motors have error, generally the lower error the better. Step error is measured in increments of arc-minutes, where 1 arc-min equals 1/60°, or 0.0167°. The industry average error for a 0.9° stepmotor at 64× microstepping is 4.5 arc-min, or 0.075°.
Smooth Steps
Smooth Steps
At certain speeds, stepmotors can resonate and vibrate loudly. This vibration translates into jerky motion. The loud noise is due to the rotational frequency matching the motor’s inherent resonant frequency. Two major factors determine a stepmotor’s resonant speed: torque stiffness and inertia.
Reliability
Reliability
Mean-time-between failure (MTFB) will help determine a motor reliability. The name should give away what this metric measures: the mean time between failures of the motor. Stepmotors typically have an MTBF of over 20,000 hr of continuous operation When stepmotors operate within their radial load at temperatures < 50C, they can last 20 years (assuming 50% duty cycle).
Speed
Speed
The motor you choose can depending on the number of RPMs you need. Generally, brushless DC motors are better for devices that require higher RPMs.
Choosing the right motor
With all the different motors we described: AC vs DC, Servo vs stepper, Brushed vs brushless, what motor is right for the job you are trying to accomplish? The following tables show a comparison of DC motors (Table 5.3.1) and a comparison of AC and DC motors (Table 5.3.2).
Table 5.3.1
Comparison of DC motors
Brushed DC Motor | Brushless DC Motor | Stepper Motor | |
---|---|---|---|
Advantages |
|
|
|
Disadvantages |
|
|
|
Table 5.3.2
Comparison of AC and DC motors
AC Motor | DC Motor | |
---|---|---|
Commutator | No | Yes |
Supply Phase | Can use single and three-phase supply | Only single-phase supply |
Terminals | Three input terminals | Two input terminals – Positive and negative |
Brushes | No | Yes – depending on the type of DC motor |
Starter | Not self starting. Requires external starting equipment | Self starting |
Position of armature | Stationary armature, magnetic field rotates | Magnetic field stationary, armature rotates |
Applications | Large and industrial applications | Used in small and domestic applications |
Maintenance | Less expensive compared to DC motors | More expensive compared to AC motors
|
Troubleshooting Motors
To state the obvious, the wiring is quite important in motors. Without wires the motor wouldn’t work. What may be of more importance to you is that if you connect the wires improperly the motor will not function as indicated. For example: in a three phase AC motor, if you change the phase (interchange the wiring of any 2 phases), the motor will rotate in opposite direction.
Another tip: Never attempt to rewind or place a solder bridge across an open winding. If the windings are shorted, then replace the motor.
Now we will go through some common problems associated with motors and discuss how to fix them. The solutions are typically for larger, more expensive motors. If the motor is small and cheap, it may be more cost and time effective to simply replace the whole motor.
Problem: Motor has no power. Power indicator light does not come on
The following are three common power issues with motors, how to diagnose the issue and a solution to each problem.
Likely causes: Motor has no power, motor has been mis-wired, motor is damaged
1. Check the power cord for continuity
- Switch voltmeter to resistance or continuity setting
- Place one lead of DMM on the plug tip and the other lead on the corresponding color wire coming into the motor
- If there is large or infinite resistance, the power cord is bad
Solution: replace power cord
2. Check wall for available power
- Switch voltmeter to AC voltage setting
- Place one lead in socket (not ground) and the other lead into the socket next to it (not ground). You may place either lead in either socket as the measured AC voltage will be the same as long as you leave the ground untouched
- Voltmeter should read 110-120 VAC
Solution: if no voltage is present, report outage to physical plant and move the apparatus to a near functioning outlet
3. Check on/off switch
- With the switch in the on position and the device unplugged, measure the resistance across the switch
Solution: replace switch
Problem: Motor has no power. Power indicator light is ON
For DC motors: Check the brushes
- On most brushes there will be ‘wear line’ indicating required length of the brushes to provide proper contact. If the brushes wear past this point, they will not make proper contact
- If there is noticeable wear on the armature the motor must be replaced
Solution: If there is no noticeable wear, replace the brushes. Run the motor for 5 minutes to provide proper seating of the brushes
For AC motors: Check the hot and neutral wires to the stator
- Using your DMM, select AC voltage
- Place the red lead on either the hot or neutral wire and connect the black wire to the ground from the power cord or chassis ground
- Your DMM should read house voltage
Solution: If there is no voltage, the wire from the motor housing to the contact terminal is open and must be replaced
For AC motors: Check for debris preventing proper magnetic field strength
- Motors are frequently lubricated and the lubricant will trap dust particles. Over time, this build-up will prevent proper conduction. Overheating of the motor is a result of this build-up.
Solution: clean the motor with a clean, lint-free cloth. Apply lubricant were indicated. Do not use solvents (alcohol) to clean the motor as this may remove the lacquer coating for the winding. For centrifuges/compressors, ensure there is proper ventilation around the device. This will lessen the occurrence of build-up and overheating.
Problem: Motor has previously worked but is no longer working
Likely causes: motor is no longer receiving power or if the motor is overloaded, fuse/circuit breaker has tripped, stator has shorted, capacitor or starting switch may have failed
What to do?
Check to see if the motor is receiving power by following the steps above. Also, determine that the amperage drawn by the motor is acceptable based on the namplate rating. If a fuse or circuit has tripped, simply replace the fuse or reset the circuit breaker. To determine if a stator has shorted, you will need to disassemble the motor and inspect the internal windings/conncections. A shorted stator will show a burn mark. If you see this, the best course of action is usually replacing the motor. To check the capacitor, you must first discharge it. Set your multimeter to RX100 scale and connect probes with capacitor terminals. If your multimeter moves to 0Ωs and drifts back to high, then the capacitor is likely working as intended. If the meter remains at 0Ωs, this indicates a short. If the meter displays consistent high Ωs, this indicates an open circuit. To determine if there is an issue with the starting switch, you must disassemble the motor. Visually inspect both the centrifugal and stationary switches. Look at the contacts and connections on the stationary switch and ensure it is not loose on the shaft. The centrifugal weights should also move easily. Replace switch if contacts are burned or potentially replace the entire motor.
Problem: Motor is working but then stops
Likely causes: the load increased or there is a voltage drop.
What to do?
Use your multimeter to determine that the load has not changed or determine if the voltage is <10% of the motor’s rating contact power.
Problem: Your motor is running in the wrong direction
Likely Cause: wiring issue
What to do?
This is an easy one. Check the schematic, fix your mistake and rewire the motor accordingly.
Problem: Motor has excessive vibration
Likely Causes: misaligned or out of balance load, rotor out of balance, defective bearings, defective windings
What to do?
If the motor is misaligned, simply realign it. If the load is out of balance, check the motor itself to ensure the motor shaft is still straight. The same advice applies to a rotor out of balance: check the motor itself. If the rotor feels rough but the bearings appear functional, the rotor will have to be replaced or rebalanced. Finally, if you suspect the motor has defective windings, test the windings to determine if they have shorted or if there is an open circuit. Your best course of action here is to replace the motor or rewind the stator.
Problem: Overheating
Likely Causes: high or low power supply voltage, friction between stator and rotor, frequent motor starting or frequent reversal of rotation
What to do?
Ensure the voltage to the motor is within the standards set forth by the manufacturer. You may simply need to reduce the amount of times you are starting the motor or reversing its direction.
Practical Troubleshooting
There are two motors in this diagram. Pick one. This motor is not rotating at all. Troubleshoot all the problems that could lead to the motor not working.
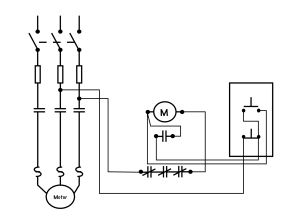
Attributions
- Figure 5.3.1 – Wiring Diagram from Basic Motor Control by Aaron Lee and Chad Flinn is licensed under CC BY 4.0