8.2 Risks That Affect Supply Chain Operations
Supply chain operations are inherently complex and susceptible to various risks that can disrupt the flow of goods and services. Understanding these risks is crucial for developing strategies to mitigate them and ensure business continuity. The primary risks affecting supply chain operations can be categorized into several key areas; some are internal to organizations, and some are external.
Variations in Demand
In today’s dynamic market environment, consumer demand is changing at an unprecedented pace, driven by evolving needs, preferences, and an ever-expanding array of options. This volatility in demand presents significant challenges for supply chain management as accurately predicting consumer behaviour becomes increasingly complex. For postgraduate students studying risk management, understanding the implications of demand fluctuations and developing strategies to address them is essential.
The impact of demand fluctuations: Accurate demand forecasting is critical for maintaining profitability and operational efficiency. Misjudging demand can lead to either excess inventory, which ties up capital and increases storage costs, or stockouts, which result in lost sales and diminished customer satisfaction. Both scenarios can have a detrimental impact on a company’s bottom line and market reputation (McGrath & Jonker, 2024).
Natural Disasters
Natural disasters have increasingly become a significant threat to global supply chains, causing widespread disruptions and economic losses. Events such as earthquakes, hurricanes, floods, and wildfires can severely impact the flow of goods and services, leading to delays, increased costs, and shortages. The frequency and intensity of these disasters have been rising, partly driven by climate change, which exacerbates extreme weather conditions.
For instance, the Texas freeze in February 2021 caused the worst involuntary energy blackout in U.S. history, leading to the closure of major semiconductor plants and exacerbating a global semiconductor shortage. Similarly, heavy rainfall and snowmelt in Europe disrupted shipping on the Rhine River, a critical commercial waterway, affecting both inbound raw materials and outbound product deliveries. In China, severe flooding in July 2021 forced the closure of a Nissan plant, highlighting the vulnerability of manufacturing hubs to natural disasters (Leslie, 2022).
The economic impact of these disruptions is substantial. The cost of addressing damage caused by natural disasters has risen from approximately $50 billion per year in the 1980s to around $200 billion per year in the last decade (Al Kazimi & Mackenzie, 2016). This trend underscores the need for robust risk management and contingency planning in supply chain operations. Effective risk management processes involve creating contingency plans to mitigate the effects of these events.
Recent data shows a concerning upward trend in the frequency and severity of natural disasters. The number of billion-dollar weather and climate disasters in the United States has increased dramatically. In 2023, there were 28 such events, surpassing the previous record of 22 in 2020. These disasters resulted in a total cost of at least $92.9 billion (USAFacts Team, 2024).
These statistics underscore the growing importance of robust risk management and contingency planning in supply chain operations. As the frequency and intensity of natural disasters continue to rise, businesses must adapt their strategies to ensure resilience in the face of these increasing global events.
Global Events
Global events, particularly political and economic developments, have become increasingly significant factors affecting supply chains and global trade. These events can range from geopolitical instability and wars to trade disputes, strikes, and fluctuations in currency values and fuel prices. The impact of such events on global markets and supply chains necessitates robust risk management processes and contingency planning.
Geopolitical tensions and conflicts have emerged as key determinants of global economic performance. The ongoing war in Ukraine and the conflict between Israel and Hamas in the Middle East, compounded by Houthi missile attacks in the Red Sea, have significantly disrupted trade flows and caused supply chain problems even in third-party countries. These events have led to higher inflation, lower growth, and significant welfare losses globally (Kaya, 2024).
Trade disputes and protectionist policies have also become more prevalent. For instance, the tariff war between the United States and China in 2018 led to a series of retaliatory measures, affecting global trade patterns and supply chains. Such disputes can lead to increased restrictions, disrupt trade flows, and cause supply chain problems that extend beyond the directly involved countries (S&P Global, n.d.).
Currency fluctuations pose another significant risk to global trade. The value of currencies can be affected by various factors, including political events and economic policies. For example, the 2022 French presidential elections correlated with a substantial drop in the Euro’s value, demonstrating how political events can influence currency dynamics.
Supplier Risk in Supply Chains
Supplier risk is a critical concern in the complex landscape of global supply chains. Healthy supply chains depend on robust supplier partnerships, but weaknesses in these relationships can introduce significant instability and vulnerability.
Key forms of supplier risk include:
- Financial Instability: Suppliers facing financial difficulties may struggle to maintain production levels or fulfill orders, potentially leading to sudden supply disruptions.
- Capacity Constraints: Limitations in a supplier’s ability to scale production can result in delays and unfulfilled orders, impacting the buying company’s operations.
- Quality Issues: Inconsistent or subpar quality from suppliers can lead to product recalls, brand damage, and increased costs.
- Geopolitical Factors: Suppliers in politically unstable regions may face disruptions due to conflicts or trade restrictions, interrupting supply flows.
- Natural Disasters: Suppliers in disaster-prone areas risk prolonged production stoppages and severe supply chain disruptions.
- Compliance and Ethical Concerns: Non-compliance with regulations or ethical standards by suppliers can expose the buying company to legal risks and reputational damage.
- Technological Obsolescence: Suppliers lagging in technological advancements may fail to meet changing product specifications or quality standards.
- Single-Source Dependency: Relying on a single supplier for critical components creates significant vulnerability, with any issues potentially causing immediate and severe impacts.
The consequences of these risks include production delays, increased costs, lost revenue, and damage to brand reputation. The interconnected nature of modern supply chains means that problems with even a single supplier can have cascading effects throughout the entire network. Understanding and addressing supplier risk is crucial for ensuring the resilience and sustainability of supply chains in an uncertain global environment (Lobdell, 2023; Vicente, 2023; Marotta, n.d.).
Cybersecurity Threats in Supply Chains
Modern supply chains heavily rely on digital systems and communication technologies for managing orders, inventory, and distribution. This digital integration, while efficient, exposes supply chains to significant cybersecurity risks.
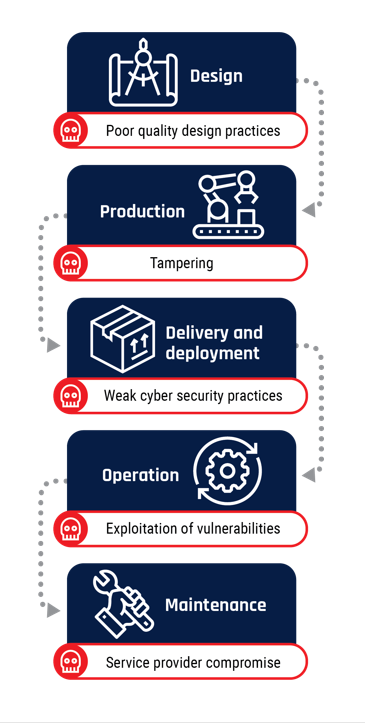
Image Description
The five areas are:
- Design – poor quality design choices
- Production – tampering
- Delivery and Deployment – weak cyber security practices
- Operation – exploitation of vulnerabilities
- Maintenance – service provider compromise
Key cybersecurity threats include:
- Ransomware and Malware Attacks can halt production and delay distribution, causing operational disruptions and financial losses.
- Data Breaches: Unauthorized access to sensitive supply chain data can expose proprietary information or customer data, leading to reputational damage and legal consequences.
- Disruption of Logistics: Cyberattacks can target transportation and logistics networks, causing delays in the distribution of goods.
- Critical Infrastructure Damage: Attacks on key infrastructure components can lead to widespread supply chain disruptions.
- Intellectual Property Theft: Cybercriminals may steal valuable IP, causing competitive disadvantages.
- Counterfeit Products: Cyberattacks can facilitate the creation and distribution of counterfeit goods, undermining brand integrity.
- Financial Fraud: Supply chains are vulnerable to cyber-enabled financial fraud, resulting in monetary losses.
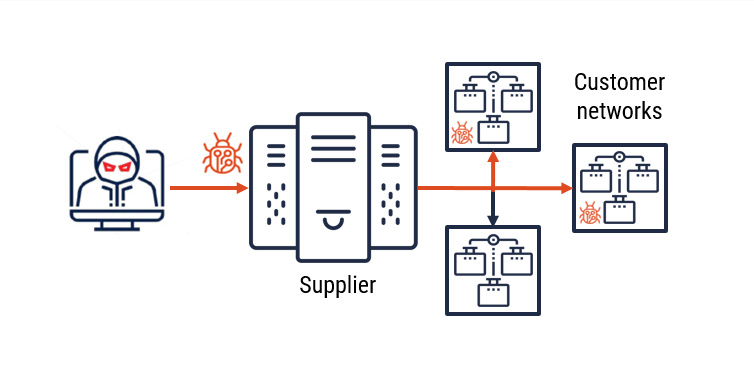
The interconnected nature of modern supply chains means that a cyberattack on one part can have cascading effects throughout the entire network. As organizations strengthen their own cybersecurity, vulnerabilities within the supply chain become critical weak points. Understanding and addressing these cybersecurity risks is crucial for maintaining the resilience and integrity of supply chains in the digital age (Canadian Centre for Cyber Security, 2023; Kost, 2023).
Ethical and Social Responsibilities
Supply chain visibility is crucial for identifying unethical practices related to human rights, labour violations, and environmental impact. Suppliers deviating from international standards or a company’s values can have significant consequences for all parties involved.
Key ethical concerns include:
- Human Rights Violations: Issues like child labour and unsafe working conditions.
- Labour Violations: Unfair practices such as underpayment and excessive working hours.
- Environmental Impact: Harmful practices like improper waste disposal and excessive emissions.
These unethical practices can lead to:
- Reputational damage
- Legal consequences
- Financial losses
Companies must prioritize ethical considerations to mitigate risks and uphold their social responsibilities, maintaining the integrity of their supply chains and protecting their reputation in an increasingly conscious marketplace (Gordon, 2023; Sedex, 2024).
Outsourcing of Operations
Outsourcing operations is a strategic approach in supply chain management that allows companies to leverage external expertise, reduce costs, and focus on core competencies. However, this strategy also introduces significant risks that must be carefully managed to ensure supply chain resilience and reliability.
Key Risks Associated with Outsourcing
- Supplier Reliability: Outsourcing depends on the reliability of external suppliers. Any weaknesses in a supplier’s financial stability, capacity, or quality control can lead to disruptions. For example, if a key supplier faces financial difficulties, it may fail to deliver critical components on time, halting production lines.
- Geopolitical and Economic Instability: Suppliers in politically or economically unstable regions pose risks. Changes in trade policies, tariffs, or political unrest can disrupt supply chains. For instance, trade tensions between the U.S. and China have increased tariffs and uncertainties for companies relying on Chinese suppliers.
- Quality Control Issues: Maintaining consistent quality standards can be challenging when operations are outsourced. Variations in quality can lead to product recalls, increased costs, and damage to brand reputation. For example, a toy manufacturer outsourcing production may face recalls if the supplier uses substandard materials.
- Intellectual Property Risks: Outsourcing can expose companies to theft of intellectual property (IP). Suppliers may misuse proprietary information, leading to competitive disadvantages. For instance, a tech company outsourcing software development may risk its code being copied or leaked.
- Compliance and Ethical Concerns: Ensuring outsourced operations comply with regulatory standards and ethical practices is crucial. Violations can lead to legal penalties and reputational damage. For example, a fashion brand outsourcing production to a factory with poor labour practices may face backlash and legal action.
- Communication and Coordination Challenges: Effective communication and coordination with outsourced partners are essential. Miscommunication can lead to delays, errors, and inefficiencies. For instance, a delay in communication about a design change can result in the production of incorrect products.
Outsourcing operations can offer significant benefits but also introduces various risks that must be managed proactively. Companies must conduct thorough risk assessments, establish robust monitoring mechanisms, and maintain strong relationships with suppliers to mitigate these risks (Schnellbächer et al., 2023; Mbiam, 2023).