Chapter 09. Performing the Audit: Functional, Operational, or Business Areas
09.02. Operational Audits: Types, Processes, Risks, and Audit Programs
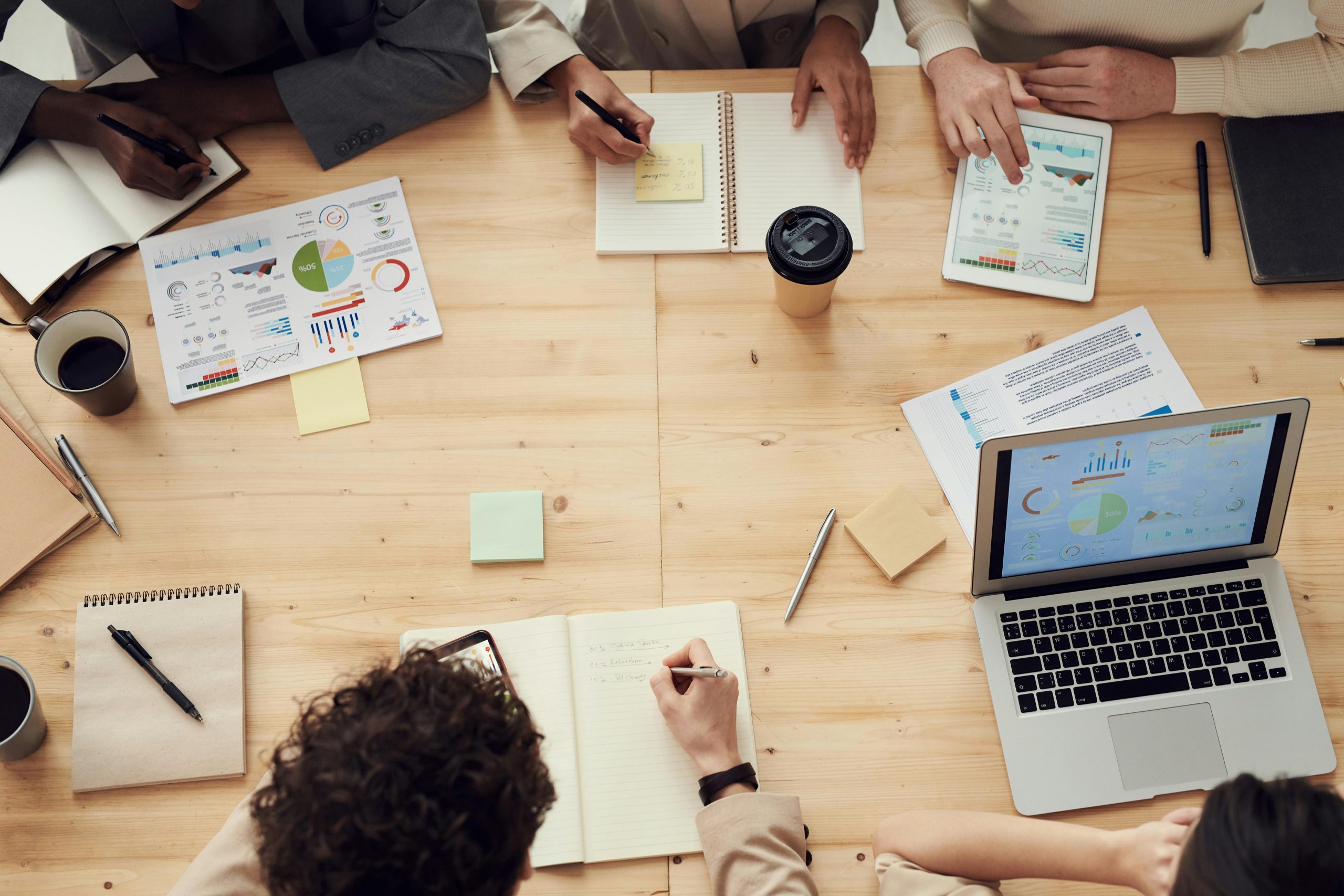
Key Questions
Briefly reflect on the following before we begin:
- How do operational audits differ from financial audits in scope and objectives?
- What key risks are associated with operational processes, and how can they be audited effectively?
- How can auditors identify opportunities for process improvements during operational audits?
- What role do Key Performance Indicators (KPIs) play in operational audits?
Operational audits are a pivotal aspect of organizational oversight, focusing on the efficiency and effectiveness of operational processes. This section delves into the core components of operational auditing, with a definition that delineates the scope and objectives of an operational audit. Auditors scrutinize operational processes to evaluate their efficacy, identifying inefficiency or potential improvement areas.
KPIs and benchmarking are central to operational audits, providing metrics for performance assessment and comparison against industry standards or organizational targets. By benchmarking operational performance, auditors gain insights into areas of strength and areas needing enhancement. Moreover, operational audits uncover process improvement opportunities, offering recommendations to streamline workflows and enhance productivity. Supply chain and logistics operations represent critical focal points within operational audits, as auditors assess the efficiency and effectiveness of these interconnected processes. Techniques for auditing outsourced operations are also explored, ensuring that external partners adhere to contractual agreements and uphold organizational standards. Through meticulous reporting, auditors communicate findings and recommend operational improvements, facilitating organizational growth and resilience.
Internal Audit in Action
Background
Tobi Eco Packaging, a manufacturer of eco-friendly packaging solutions, has seen a decline in operational efficiency over the past year, leading to increased costs and reduced competitiveness. The internal audit department initiated an operational audit focusing on manufacturing processes and supply chain management to address these issues.
Challenge
The challenge was to identify inefficiencies and bottlenecks in Tobi Eco Packaging’s operational processes, assess the effectiveness of current operational controls, and provide actionable recommendations for improvement.
Action Taken
- Defining Operational Auditing Objectives: The audit objectives evaluated the efficiency and effectiveness of manufacturing processes and supply chain operations, aiming to identify areas of waste, inefficiency, and potential cost savings.
- Evaluating Efficiency and Effectiveness: The audit team comprehensively evaluated the entire production lifecycle, from raw material procurement to product delivery, using KPIs and benchmarking against industry standards.
- Identifying Process Improvement Opportunities: Through detailed process mapping and analysis, the team identified several critical areas for improvement, including inventory management, production scheduling, and supplier performance.
- Auditing Supply Chain and Logistics Operations: Special attention was given to the supply chain and logistics operations, where delays and inefficiencies contributed to increased lead times and customer dissatisfaction.
- Reporting and Recommending Operational Improvements: The audit concluded with a report that detailed findings and recommended specific operational improvements, such as adopting just-in-time inventory practices and implementing supplier performance management systems.
Outcome
Tobi Eco Packaging’s management team implemented the recommendations from the operational audit, resulting in significant improvements in manufacturing efficiency, reduced costs, and enhanced customer satisfaction. The audit highlighted areas for immediate improvement and provided a framework for ongoing operational excellence.
Reflection
Tobi Eco Packaging’s scenario demonstrates the value of operational audits in identifying inefficiencies and improving organizational performance. By focusing on specific operational areas and employing a structured approach to evaluate processes and controls, internal audit functions can provide critical insights and recommendations that drive operational improvements and contribute to strategic goals.
Defining Operational Auditing: Scope and Objectives
Operational auditing is an integral process conducted by internal auditors to evaluate the effectiveness, efficiency, and economy of an organization’s operations. Unlike financial auditing, which is primarily concerned with verifying financial records and ensuring compliance with accounting standards, operational auditing focuses on examining an organization’s operational aspects to identify areas for improvement and add value to the business. This type of auditing is comprehensive, extending its reach across various departments and functions, and is designed to enhance overall operational performance.
Scope
The scope of operational auditing is broad and not confined to any specific department or function. Instead, it encompasses all areas where improvements can be made to bolster operational effectiveness and efficiency. It includes the following:
- Examining business processes and systems to ensure they are optimally designed and functioning effectively. Auditors review these processes to ascertain whether the organization’s products or services are being produced efficiently and if there are opportunities for process optimization.
- Assessing the utilization of resources such as workforce, materials, equipment, and technology. This assessment determines whether these resources are used efficiently and effectively.
- Evaluating the organizational structure to ensure it efficiently supports its goals and objectives.
- Examining how well the organization identifies, manages, and mitigates operational risks, i.e., risk management.
- Scrutinizing internal controls related to operational processes to ensure they are adequate and functioning as intended.
Objectives
The objectives of operational auditing are multifaceted, primarily aimed at providing assurance, offering recommendations for improvements, and fostering organizational learning and development. Some of the main goals of operational auditing include the following:
- Improving operational efficiency by identifying inefficiencies in processes and recommending changes that reduce waste, shorten cycle times, and lower costs without compromising quality.
- Enhancing effectiveness by assessing whether the outcomes of business processes align with the organization’s goals and determining whether these processes are achieving their intended results.
- Ensuring compliance with relevant laws, regulations, and internal policies, extending beyond financial compliance to operational adherence.
- Identifying new or changing risks that could impact the organization’s operations and evaluating whether current controls adequately mitigate these risks.
- Encouraging continuous improvement initiatives within the organization by providing constructive feedback on operations, thereby promoting a culture of efficiency and adaptiveness.
To achieve these objectives, operational auditing employs a variety of techniques. Techniques include the following:
- Process mapping is commonly used to create detailed flowcharts of processes, helping identify unnecessary steps, bottlenecks, or control weaknesses.
- Benchmarking is another critical technique for comparing organizational practices with other organizations’ best practices to pinpoint improvement areas.
- Interviewing colleagues and employees and observing processes to gain insights into the day-to-day workings and challenges of different departments.
- Utilizing risk assessment tools such as SWOT analysis (Strengths, Weaknesses, Opportunities, Threats) or risk matrices to identify and prioritize risks systematically.
Thus, operational auditing is essential for compliance and a deeper understanding of organizational processes and their effectiveness. Operational auditors can align their activities with the organization’s strategic goals, providing valuable insights and recommendations that significantly improve operational efficiency and effectiveness by clearly defining its scope and objectives. This proactive approach not only supports better management decisions but also enhances the overall performance and sustainability of the organization, thereby ensuring its long-term success.
Evaluating Efficiency and Effectiveness of Operational Processes
Evaluating the efficiency and effectiveness of operational processes is crucial in operational auditing, where the primary focus is on how an organization utilizes its resources and conducts activities to achieve specified goals. It helps auditors identify areas for improvement and recommend strategies that enhance overall performance.
Through detailed audits of operational efficiency and effectiveness , organizations can fine-tune their operations, reduce costs, improve customer satisfaction, and ultimately enhance overall performance.
This systematic approach not only supports better management decisions but also boosts the organization’s competitiveness and sustainability in the long term.
Operational Efficiency
This assesses how well an organization uses resources to achieve objectives with minimal waste, effort, or expense.
It involves streamlining processes, optimizing resource utilization, and reducing costs and includes the following activities:
- Auditors examine resource utilization by reviewing how personnel, technology, and materials are used in business processes.
- Auditors analyze resource allocation, workload distributions, and output rates to pinpoint overuse or underutilization.
- Auditors also look at process streamlining by identifying redundancies, bottlenecks, and unnecessary complexities that could slow down operations or increase costs, suggesting modifications to simplify and accelerate workflows without compromising quality.
- Auditors review cost efficiency by checking if the organization achieves its objectives at the lowest possible cost, which involves reviewing adherence to budget and cost control measures and comparing them with industry benchmarks.
- Auditors evaluate time management by checking the time taken for processes and activities, identifying delays, and recommending ways to reduce cycle times to enhance responsiveness and customer satisfaction.
Operational Effectiveness
While efficiency focuses on resource usage, effectiveness concentrates on the outcomes of business activities to ascertain whether organizational goals are being met. Operational effectiveness includes the following activities:
- Auditors check goal alignment to ensure operational processes align with the organization’s strategic objectives, confirming that every activity adds value toward achieving these goals.
- Auditors use performance indicators to measure the outcomes of various processes, including metrics like customer satisfaction scores, product quality, or market share analysis.
- Auditors evaluate the effectiveness of each department or process by determining the success rates of their projects, initiatives, and day-to-day operations.
- Auditors assess how feedback is collected and utilized to improve services or products, as effective feedback mechanisms are crucial for continuous improvement and adapting to changing market demands.
Techniques
To effectively evaluate efficiency and effectiveness, auditors employ the following techniques:
- KPIs and other metrics help to quantitatively assess how healthy processes perform against expected standards.
- Comparative analysis is utilized to compare the organization’s performance with industry standards or best practices to understand operational excellence.
- Direct observations of workflows and interviews with staff at all levels provide insights into the practical challenges and successes of operations.
- Surveys and questionnaires are used to gather feedback from employees and customers to understand their views on the efficiency and effectiveness of the processes they interact with.
Key Performance Indicators (KPIs) and Benchmarking in Operational Audits
Key Performance Indicators (KPIs) and benchmarking provide auditors with measurable data to evaluate the performance of business processes and functions and help organizations track their efficiency, effectiveness, and alignment with strategic objectives. Insights gained from KPIs and benchmarking reflect current performance and align with strategic goals. These insights guide strategic decision-making and help set realistic performance goals aligned with industry standards.
By regularly checking KPIs and reviewing benchmarking results, organizations can monitor progress and adapt their strategies and operations to continuously improve their competitive position.
Key Performance Indicators (KPIs)
KPIs are quantifiable measurements that reflect an organization’s critical success factors and vary significantly depending on the industry, specific operational area, and strategic goals.
Auditors use KPIs to conduct a detailed analysis of operations and identify trends, variances, and patterns that might indicate problems or opportunities for improvement. As such, in operational audits, KPIs measure different aspects of operations, providing a clear basis for evaluating success and pinpointing areas of improvement.
For KPIs to be effective in an audit context, they must be SMART— Specific, Measurable, Achievable, Relevant, and Time-bound. Auditors verify the accuracy of KPI data and assess whether the KPIs are appropriately aligned with the organization’s strategic objectives, ensuring they provide meaningful insights into performance and opportunities for improvement. The three different types of KPIs are:
- Financial KPIs: These might include cost per unit, profitability margins, or return on investment (ROI), which assess an operation’s economic efficiency and effectiveness.
- Operational KPIs: These could encompass production rates, quality rates, inventory turnover, or customer service response times, focusing on the business’s day-to-day operations.
- Strategic KPIs: These track the achievement of broader organizational goals, such as market share growth, employee engagement levels, or innovation rates.
Benchmarking
Benchmarking involves comparing an organization’s performance metrics with those of leading competitors or similar organizations.
This comparison provides an objective perspective on performance and practices, helping auditors and management understand how well the organization is performing compared to others in the industry. Such comparison also helps to identify areas where the organization is lagging and where it excels. The types of benchmarking include:
- Internal benchmarking: This compares operations within various departments or divisions of the same organization to share best practices and standardize processes where possible.
- Competitive benchmarking: This involves comparing the organization’s processes and performance with direct competitors to gauge its industry position.
- Functional benchmarking: This looks at specific functions or operations, comparing them with those of industry leaders or innovators, even if they are in different sectors.
- Generic benchmarking: This broadens the scope by comparing similar business functions and processes across industries, such as supply chain management or human resources practices.
Identifying Process Improvement Opportunities
Operational audits offer opportunities for process improvement. These audits involve a thorough analysis of existing processes, allowing auditors to pinpoint inefficiencies, redundancies, and areas needing enhancement or complete re-engineering.
The process begins with a comprehensive understanding of the current processes. Key activities in this initial stage include operational process mapping, data collection, and workflow analysis.
- Process mapping involves creating detailed diagrams that visualize the flow of activities, helping to identify complex or unnecessary steps that could be streamlined.
- Data collection encompasses quantitative and qualitative data gathered through observations, interviews, and document reviews, providing a baseline for measuring process performance.
- Workflow analysis examines the sequence of operations within a process to determine bottlenecks, delays, or frequent error points.
Once the current processes are analyzed, auditors study the performance to identify areas that fail to meet their potential. This analysis includes:
- Evaluating efficiency metrics—such as the time, resources, and inputs required to produce outputs—where high resource consumption or slow performance might indicate areas ripe for improvement.
- Evaluating effectiveness metrics to see whether the processes achieve their intended goals, with indicators like low customer satisfaction, high defect rates, or failure to meet service levels highlighting processes needing corrective actions.
- Benchmarking—comparing the organization’s processes to industry best practices can reveal gaps in methods or technologies.
With a clear understanding of process performance, auditors can identify specific opportunities for improvement. This typically involves processes that achieve the following goals:
- Eliminating waste by identifying and removing activities that do not add value, such as excessive approvals, redundant data entry, or unnecessary steps in a process.
- Improving quality, which might include implementing quality control checks or adopting more robust procedures or technologies.
- Streamlining processes to make them faster and more cost-effective, which can involve automating manual tasks, reordering process steps for better workflow, or consolidating tasks to reduce handoffs.
In some cases, where incremental improvements are insufficient, complete process re-engineering may be necessary. This could involve adopting new technologies, redesigning workflows, or fundamentally changing how a service or product is delivered.
Technology solutions play a crucial role in facilitating process improvement. Auditors often recommend technologies that automate repetitive tasks, improve data accuracy, and enable faster decision-making. Technology can provide the following solutions:
- Automation tools can handle routine tasks like data entry or report generation, freeing up employees for higher-value activities.
- Advanced analytics tools provide deeper insights into process performance and predict future trends, helping organizations make informed improvements.
- Additionally, collaboration platforms can enhance communication and collaboration across departments, improving process integration and efficiency.
By systematically analyzing existing operations and employing innovative solutions, auditors can help organizations realize significant performance enhancements. These improvements lead to cost savings, better resource utilization, improved customer satisfaction, and a competitive advantage, ensuring long-term sustainability and success.
Auditing Supply Chain and Logistics Operations
Supply chain auditing and logistics operations auditing focus on the flow of goods and information from suppliers to customers. Its intention is to identify risks, inefficiencies, and non-compliance with regulatory standards. Let’s explore the methodologies and focus areas auditors consider when assessing supply chain and logistics operations, providing a structured approach to enhancing organizational resilience and operational efficiency.
The scope of supply chain and logistics audits spans the following key areas:
- Supplier management involves evaluating processes for selecting and managing suppliers. This includes assessing how relationships with suppliers are maintained, how suppliers are evaluated, and the criteria used for their selection.
- Inventory management involves assessing methods used for managing inventory, including the accuracy of inventory records, inventory turnover efficiency, and the effectiveness of inventory forecasting.
- The transportation and distribution mechanisms used to move goods from suppliers to customers are reviewed, focusing on various aspects of distribution efficiency including cost efficiency, timeliness, and reliability.
- Compliance of supply chain operations with relevant laws and regulations, such as customs regulations, safety standards, and environmental laws, is reviewed.
Key focus areas for auditors seeking to ensure that supply chain and logistics operations meet organizational standards and objectives include risk management, cost control, process efficiency, quality control, and sustainability practices.
- Risk management involves identifying risks associated with supply chain disruptions, such as supplier failures, logistical delays, or regulatory non-compliance, and assessing how well these risks are identified, monitored, and mitigated.
- Cost control evaluations cover transportation costs, warehousing fees, and the cost of holding inventory, with auditors looking for opportunities to reduce costs without compromising quality or customer service.
- Process efficiency is analyzed through metrics like lead times, fulfillment rates, and the effectiveness of logistics operations.
- Customer satisfaction auditing assesses the effectiveness of quality control measures to prevent defects and ensure customer satisfaction throughout the supply chain, from initial supplier inputs to final product delivery.
- Sustainability practices are also examined, focusing on the environmental and social impacts of supply chain operations, including resource usage, waste management, and ethical sourcing practices.
Auditors employ various techniques to audit supply chain and logistics operations. These techniques include the following:
- Process mapping creates detailed maps of supply chain processes to identify redundancies, bottlenecks, or points of failure.
- Data analysis utilizes analytics to examine inventory levels, delivery times, and cost structures to identify patterns or anomalies that could indicate problems.
- Interviews and surveys with supply chain managers, logistics staff, and suppliers provide insights into operations and challenges.
- Physical inspections involve site visits to warehouses, distribution centres, and supplier facilities to observe operations firsthand and verify compliance with standards.
- Benchmarking compares the organization’s supply chain performance with industry best practices to pinpoint areas for improvement.
Thus, auditing supply chain and logistics operations is essential for maintaining operational resilience, cost efficiency, and regulation compliance. Auditors can identify risks and inefficiencies that impede organizational performance through detailed assessments. Addressing these issues enables organizations to enhance their supply chain and logistics operations, improving service levels, reducing costs, and gaining a competitive advantage in the marketplace. This proactive approach supports operational goals and aligns with strategic business objectives, ensuring long-term sustainability and success.
Auditing Outsourced Operations
Outsourced operations are crucial to the business models of many organizations, allowing them to leverage external expertise, reduce costs, and focus on core competencies. However, outsourcing also presents control, compliance, and quality risks, requiring rigorous auditing to ensure these arrangements meet organizational standards and objectives. These are some of the typical tasks that auditors need to perform to successfully audit outsourced operations:
- Before beginning an audit, auditors must fully understand the nature of the outsourcing relationships. This includes the scope of the outsourced services, the roles and responsibilities of all involved parties, and the terms of the outsourcing agreements.
- Auditors review the contracts or service-level agreements (SLAs) to grasp the expected service levels, deliverables, and compliance requirements. This review is critical to identify the KPIs that need monitoring.
- Additionally, auditors assess the risks associated with the outsourcing arrangements, such as dependency on third-party vendors, the potential for non-compliance with regulations, and data security and privacy risks.
Several specific techniques are employed to audit outsourced operations. These include the following:
- Performance audits involve evaluating the performance of the outsourced provider against the agreed-upon KPIs and SLAs. This includes checking whether the provider meets deadlines, achieves quality targets, and adheres to budget constraints.
- Compliance audits are crucial, especially in finance, healthcare, and data management sectors, where non-compliance can result in significant penalties. These audits ensure that the outsourced provider complies with industry standards and regulatory requirements.
- Process audits examine the provider’s service delivery processes, assessing their internal controls, data handling practices, and other operational procedures to ensure alignment with the client’s standards and expectations.
- Third-party audits and certifications play a role, with auditors relying on audits conducted by independent third parties or requiring certifications like ISO standards to verify the provider’s adherence to industry best practices.
- Interviews and surveys with organizational stakeholders interacting with the outsourced provider can also provide insights into any issues or dissatisfaction that may not be apparent through quantitative metrics alone.
- Site visits to the provider’s facilities are often crucial, especially for operations that involve critical data, high-value assets, or complex processes.
- Continuous monitoring and regular communication between the outsourcing client and the provider are essential for managing the outsourcing relationship effectively. This includes establishing regular reporting mechanisms and routine meetings to discuss performance, challenges, and future needs. Such ongoing dialogue helps preempt potential issues and fosters a proactive approach.
- Technology solutions that allow real-time monitoring of outsourced operations can provide immediate insights into performance and help quickly rectify deviations from expected standards.
- As business environments and external conditions change, the risks associated with outsourced operations can also evolve. Regular updates to risk assessments and adapting audit strategies are essential for effective oversight.
Auditing outsourced operations requires a comprehensive approach encompassing a thorough review of contractual obligations, performance evaluation, compliance checks, and formal and informal interactions with the service provider. Effective auditing of outsourced operations reinforces compliance and performance, ensuring that strategic business objectives are met through maintaining robust and reliable partnerships.
Internal Audit in Action
Background
Pepper, a national fast-food restaurant chain, aims to enhance customer satisfaction and operational efficiency across its outlets. The internal audit department launched an operational excellence audit to assess the effectiveness of service delivery, food quality control, and cleanliness standards.
Challenge
The primary challenge was to evaluate operational practices across multiple outlets, identifying variances in service quality and operational efficiency that could impact customer satisfaction and brand reputation.
Action Taken
- Operational Audit—Scope and Objectives: The audit was scoped to include critical aspects of Pepper’s operations, including customer service processes, food preparation and quality control procedures, and cleanliness and hygiene standards.
- Evaluating Service Delivery and Food Quality: The audit team utilized a combination of mystery shopping, direct observations, and staff interviews to evaluate the consistency and quality of service delivery and food preparation practices.
- KPIs and Benchmarking: Key performance indicators were established for each area of operation, with benchmarking against industry best practices to identify gaps and areas for improvement.
- Identifying Areas of Process Improvements: The audit identified several critical areas for operational improvement, such as streamlining order processing to reduce wait times and implementing more rigorous food quality checks.
- Reporting Areas of Operational Improvements: Recommendations were provided in a detailed management report, outlining specific actions to improve customer service, enhance food quality, and maintain high standards of cleanliness.
Outcome
Implementing the audit recommendations led to notable improvements in Pepper’s operational efficiency and customer satisfaction scores. The operational excellence audit helped identify areas for immediate action and established a culture of continuous improvement and excellence within the organization.
Reflection
Pepper’s operational excellence audit underscores the importance of operational audits in enhancing customer satisfaction and achieving operational efficiency. Through a focused evaluation of service delivery and operational practices, internal audits can uncover critical insights and opportunities for improvement, driving positive changes that enhance overall organizational performance and customer experience.
Key Takeaways
Let’s recap the concepts discussed in this section by reviewing these key takeaways:
- Operational auditing enhances organizational efficiency and effectiveness by evaluating and improving various processes across departments and functions.
- Auditors use process mapping, benchmarking, interviews, and risk assessments to identify inefficiencies and areas for improvement in an organization’s operations.
- Audits assess operational processes to ensure resources are used efficiently and organizational goals are effectively met, using KPIs and performance metrics for evaluation.
- KPIs measure operational success and areas for improvement, while benchmarking compares these metrics against industry standards to guide strategic decision-making.
- Rigorous auditing of outsourced operations is essential to manage control, compliance, and quality risks, ensuring alignment with organizational standards and objectives.
Knowledge Check
Review Questions
- Explain the primary difference between operational auditing and financial auditing.
- What are the main objectives of operational auditing?
- Describe how auditors use benchmarking in operational audits.
- How do auditors assess the efficiency of operational processes?
- What techniques are employed to audit outsourced operations effectively?
Essay Questions
- Evaluate the role of risk assessment tools like SWOT analysis in operational audits and discuss how they enhance the audit process.
- Discuss the importance of process mapping in operational audits and its impact on identifying process improvement opportunities.
- Analyze how the use of technology can improve the effectiveness of operational audits, particularly in data analytics and automation.
Mini Case Study
Greene Power is a leading manufacturer of solar panels and sustainable energy solutions. The company has operations spanning multiple continents, with manufacturing plants, distribution centres, and corporate offices. Despite robust sales, recent internal reviews suggest potential inefficiencies in several operational areas, which could be impacting overall productivity and profitability. The current operational processes for the company include the following:
- Supplier Management: The company sources materials from over 100 suppliers worldwide but lacks a standardized evaluation process for supplier performance, leading to variability in material quality and supply chain disruptions.
- Inventory Management: Inventory levels fluctuate significantly, often leading to either a surplus or shortages, impacting production schedules and order fulfillment rates.
- Logistics and Distribution: Distribution strategies have not been revised in several years, and there are reports of frequent delays and customer complaints regarding delivery times and product handling.
- Compliance and Sustainability Practices: As a leader in the sustainable energy sector, compliance with environmental regulations and maintaining sustainability practices are crucial. However, no formal audit process ensures that these practices are followed uniformly across all locations.
Required: As an operational auditor hired by Greene Power, you are tasked with evaluating these operational areas to identify inefficiencies and recommend improvements to enhance effectiveness and efficiency. Address the following questions:
- Assess the current supplier management process at Greene Power. What risks can you identify, and what improvements would you suggest?
- Evaluate the inventory management system. How can the company optimize inventory levels for production needs and order fulfillment?
- Given the issues in logistics and distribution, what strategies could be implemented to improve delivery times and customer satisfaction?
- Develop a compliance audit process for the company’s sustainability practices. How should this process be structured to ensure consistent adherence across all operational locations?
The evaluation of an individual's or organization's work performance against established standards and objectives to identify strengths and areas for improvement.
Changes and enhancements made to processes, systems, or practices to increase efficiency, effectiveness, and overall performance.
Systematic approach to improving processes, workflows, or systems to enhance efficiency, quality, and performance by identifying and eliminating inefficiencies, bottlenecks, or waste using analytical methods.
The potential for loss resulting from inadequate or failed internal processes, people, systems, or external events impacting an organization's operations.
The ongoing effort to enhance products, services, or processes by making incremental changes over time to increase efficiency and quality.
The effective and efficient use of an organization's resources, such as personnel, equipment, and materials, to achieve its objectives.
The measure of how well an organization uses its financial resources to achieve its goals, minimizing costs while maintaining quality and performance.
The process of planning and exercising control over the amount of time spent on specific activities to increase efficiency and productivity.
Long-term goals set by an organization to guide its direction, drive decision-making, and achieve desired outcomes and competitive advantage.
The systematic approach to enhancing business processes to achieve more efficient results, reduce costs, and improve quality and performance.
The visual representation of an organization's processes, identifying each step and its interactions to improve understanding and efficiency.
Quantitative measures used to evaluate the effectiveness and productivity of organizational processes, activities, or resources in achieving desired outcomes or delivering value efficiently.
Quantitative measures used to assess the extent to which organizational activities achieve their intended outcomes and contribute to overall goals.
Innovative technological tools and systems designed to solve specific business problems, enhance efficiency, and support strategic objectives.
The process of reviewing and evaluating the efficiency, effectiveness, and compliance of an organization's supply chain operations and management.
The management of the flow of goods, information, and resources from origin to consumption, ensuring efficient and effective movement and storage.
The process of overseeing and controlling the ordering, storage, and use of a company's inventory to optimize efficiency and reduce costs.
The optimization of distribution processes to ensure that products are delivered to customers in the most cost-effective and timely manner.
The measure of how well a process converts inputs into outputs, focusing on minimizing waste and optimizing resource utilization.
The assessment of customer feedback and satisfaction levels to identify areas for improvement in products, services, and customer relations.
Actions and strategies adopted by an organization to minimize its environmental impact and promote social and economic sustainability.
The amount of time taken from the placement of an order to the delivery of the product to the customer, impacting customer satisfaction and operational efficiency.
Specific, measurable objectives set by an organization to guide and assess the performance of its operations and achieve strategic aims.
Business processes or services contracted out to third-party providers to enhance efficiency, reduce costs, and allow focus on core activities.
The continuous observation and analysis of systems, processes, or activities as they occur, allowing for immediate detection and response to issues.
The process of reviewing and verifying that an organization's operations, processes, and practices adhere to internal policies and external regulations.