6.3 Cost of Quality
Organizations that deliver high-quality goods and services can achieve a competitive edge and distinguish themselves in the marketplace. These companies often experience higher profitability, as they incur minimal losses and additional expenses related to poor productivity, rework, inspections, and scrap.
The costs associated with maintaining and improving quality can be categorized into four main types: prevention costs, appraisal costs, and failure costs. Failure costs are further divided into internal failure costs and external failure costs. Understanding and managing these cost categories is crucial for optimizing quality management and enhancing overall operational efficiency.
Prevention costs
Prevention costs encompass all expenditures aimed at proactively avoiding the occurrence of defects or non-conformities in products or services. These costs are incurred through initiatives such as quality improvement programs, employee training and development, equipment upgrades, implementation of quality management systems, and proactive design modifications. Investing in prevention activities can significantly reduce the likelihood of defects and associated costs further down the production process.
Appraisal costs
Appraisal costs refer to the resources dedicated to inspecting, testing, and evaluating products or services during the production or delivery process. These costs include wages for quality inspectors, expenses related to testing laboratories and equipment, gauging and measurement activities, and process control mechanisms. Appraisal activities aim to identify and eliminate defects before they reach the customer, thereby preventing potential failure costs.
Internal failure costs
Internal failure costs arise when defects or non-conformities are detected within the organization before the product or service is delivered to the customer. These costs encompass rework efforts to rectify identified defects and the costs associated with scrapping or disposing of products that cannot be repaired or reworked. Internal failure costs include potential disruptions to production schedules, expedited manufacturing efforts to compensate for scrapped products, and the associated opportunity costs.
External failure costs
External failure costs are incurred when defective products or non-conforming services reach the customer. These costs can be substantial and may include expenses related to product replacements, expedited shipping, product recalls, potential legal liabilities, and the detrimental impact on customer satisfaction and future business opportunities. External failure costs are often challenging to quantify precisely due to the intangible nature of lost customer goodwill and its long-term implications on an organization’s reputation and market position.
By understanding and effectively managing these cost categories, organizations can optimize their quality management efforts, minimize defects and non-conformities, and ultimately enhance customer satisfaction while reducing overall operational costs.
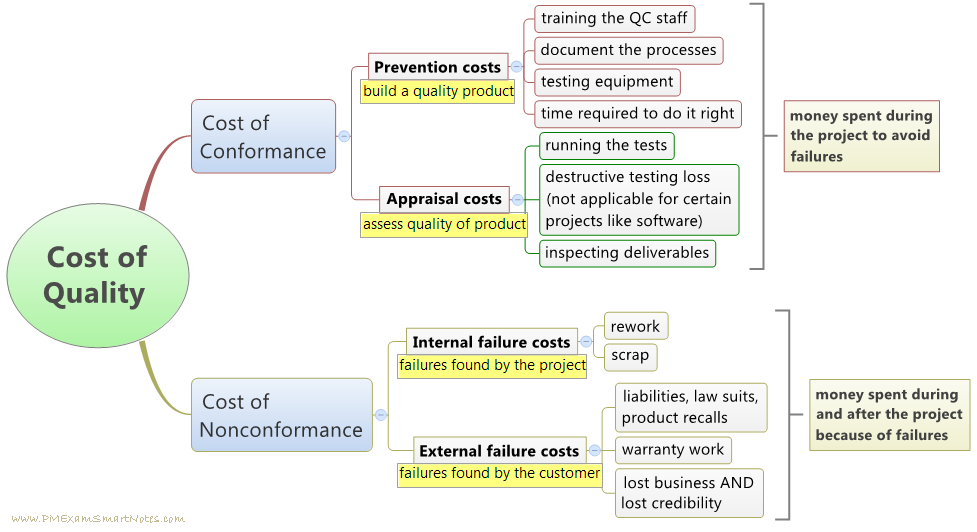
Image Description
Cost of Quality
- Cost of Conformance: Money spent during the project to avoid failures.
- Prevention Costs: Costs to build a quality product.
- Training the QC staff
- Documenting the processes
- Testing equipment
- Time required to do it right
- Appraisal Costs: Costs to assess the quality of the product.
- Running the tests
- Destructive testing loss (not applicable for certain projects like software)
- Inspecting deliverables
- Prevention Costs: Costs to build a quality product.
- Cost of Nonconformance: Money spent during and after the project because of failures.
- Internal Failure Costs: Failures found by the project.
- Rework
- Scrap
- External Failure Costs: Failures found by the customer.
- Liabilities, lawsuits, product recalls
- Warranty work
- Lost business and lost credibility
- Internal Failure Costs: Failures found by the project.
“5 Managing Quality” from Introduction to Operations Management Copyright © by Hamid Faramarzi and Mary Drane is licensed under a Creative Commons Attribution-NonCommercial-ShareAlike 4.0 International License, except where otherwise noted.—Modifications: used section Cost of Quality, some paragraphs rewritten.